Why a Granulator Maintenance Plan Pays Dividends
Unscheduled downtime, inconsistent regrind quality and spiralling blade costs all trace back to poor upkeep. Studies by major OEMs show that moving from “run-to-failure” to a structured preventive program can cut granulator downtime by 65 – 85 % and extend knife life three-fold.
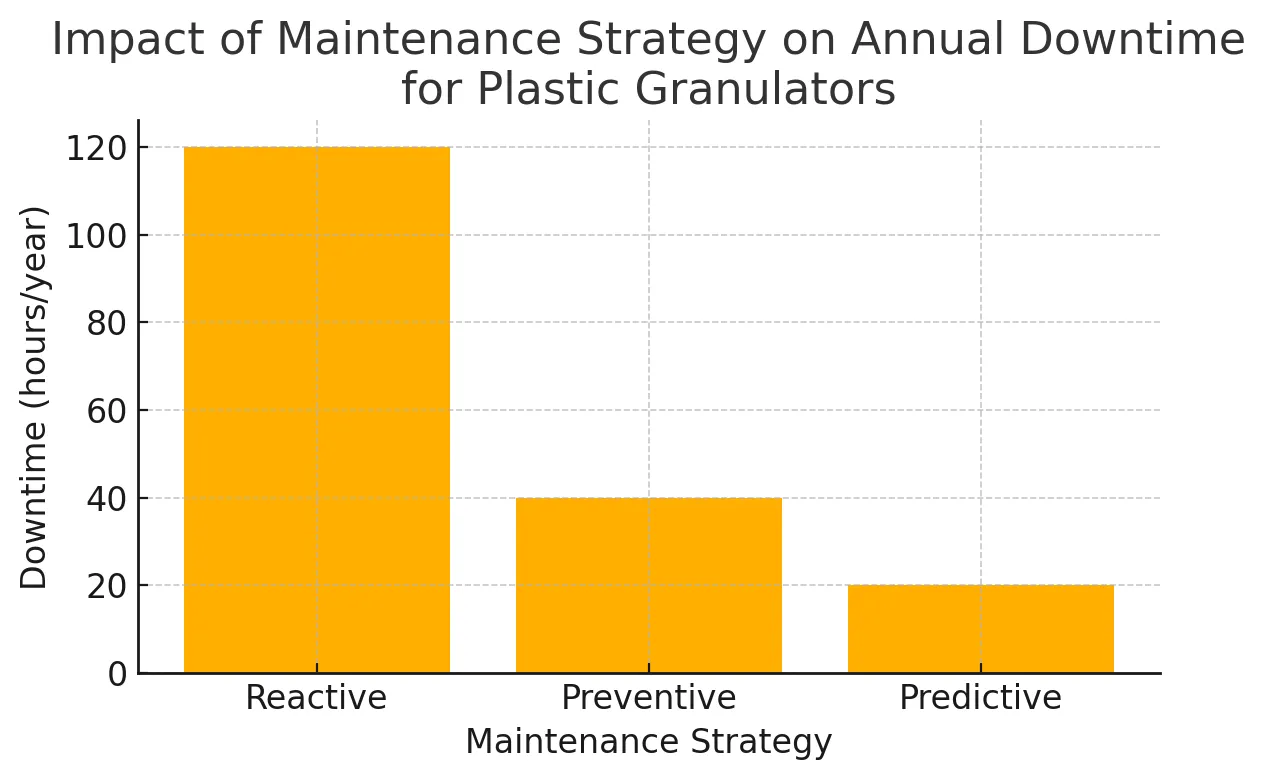
Key Business Benefits
KPI | Reactive Maintenance | الصيانة الوقائية | Predictive (sensor-based) |
---|---|---|---|
Annual downtime (hrs)** | 120 | 40 | 20 |
Knife spend (US$/t) | $9.50 | $4.20 | $3.10 |
Energy use (kWh/t) | 98 | 72 | 68 |
**See bar-chart below for a visual comparison.
Daily Checks – 5 Minutes That Save Hours Later
- Visual clean-out – Remove fines around the hopper, cutting chamber and screen to avoid heat-buildup and flash.
- Listen for noise & vibration – A sudden whine often signals knife gap drift or loose rotor bolts.
- Screen condition – Replace clogged or deformed screens immediately; even a 10 % blockage can raise motor load by 15 %.
- Motor temperature & amps – Log and trend; spikes flag dull blades or belt slippage.
- Safety interlocks – Test gate and hopper switches at shift-start.
Weekly / Monthly Preventive Tasks
Interval | مهمة | لماذا هذا مهم؟ |
---|---|---|
أسبوعي | Check drive-belt tension & wear | Loose belts waste energy and accelerate bearing wear. |
Verify knife-to-bed knife gap (0.10–0.25 mm typical) | Correct gap preserves sharp edge and reduces dust. | |
Inspect rotor bearings for grease purge | Early sign of over-lubrication or seal failure. | |
شهريا | Grease bearings (OEM-specified grease) | Prevents overheating and seizure. |
Torque-check all chamber fasteners | Eliminates vibration-induced loosening. | |
Inspect electrical cabinet: terminals, breakers | Heat discoloration indicates overload or poor contact. |
Blade & Screen Care – The Heart of High-Quality Regrind
- Sharpen before dullness is visible. A good rule: resharpen every 40–60 h for thin film, 80–100 h for thick parts. Blades can be sharpened ~10 times before replacement.
- Use a precision jig. Post-grind pitch must match OEM spec to avoid irreversible rotor damage.
- Balance and match sets. Always install knives as matched sets to keep rotor in balance and limit bearing load.
- Screen inventory. Keep two spare screens per machine; damaged apertures distort particle size and raise fines.
Dust & Contamination Control
Excess fines hurt downstream extrusion and injection. Install an inline deduster or cyclone and empty catch bins daily. Check extraction airflow; a 20 % drop doubles fines carry-over.
Motor, Gearbox & Drive System
- Belt alignment. Misalignment >2 mm cuts belt life in half.
- Gear oil sampling. Quarterly oil analysis identifies early pitting.
- Soft-start or VFD. Reduces in-rush current and mechanical shock, lengthening motor life.
Embracing Predictive Maintenance
Affordable IoT sensors make condition-based service realistic even for small plants:
Sensor | Detects | Typical Alert |
---|---|---|
Vibration (IMU) | Bearing wear, rotor imbalance | RMS velocity >6 mm/s |
Infra-red temp | Motor overheating | >90 °C stator temp |
Current transducer | Load spikes, dull knives | +15 % over baseline |
Automated alerts shift teams from firefighting to proactive knife changes, slashing unplanned stops.
Plastic Granulator Workflow – Where Maintenance Fits
The image carousel above walks through a typical granulation line, highlighting checkpoints (hopper, cutting chamber, screen deck, discharge blower). Use it as a visual aid when training operators.
Performance Impact of Maintenance Strategy
The chart below illustrates how downtime plunges as you move from reactive to predictive maintenance.
(Chart displayed above)
Use the downtime delta to build your ROI case: every hour a 75 kW granulator sits idle costs ≈ US$180 in lost throughput and labor.
Building Your Own Maintenance Schedule
- Start with OEM recommendations and adjust to your material mix (abrasive glass-filled PP vs. soft LDPE).
- Log everything – knife hours, screen changes, belt swaps. A simple spreadsheet or CMMS works.
- Train & empower operators. 80 % of failures show early symptoms that line staff can spot.
- Keep critical spares. Minimum: full knife set, two screens, drive belt kit, grease, main bearings.
السلامة أولاً
Always follow lock-out/tag-out (LOTO) before entering the cutting chamber. Verify zero stored energy – belts, flywheels and hydraulic lids can retain force even when power is off.
Conclusion – Five Takeaways
- A documented preventive plan cuts downtime by >60 %.
- Sharp, properly-gapped knives are your cheapest throughput booster.
- Belt, bearing and screen inspections take minutes; neglect costs days.
- Dust control and motor load trending improve both product quality and energy use.
- Predictive maintenance technologies are now affordable – start small with vibration sensors.
By integrating these practices, purchasers and technical teams ensure their granulator investments deliver consistent regrind quality, lower operating costs and maximum uptime.