In der Welt der Kunststoffverarbeitung und des Recyclings Kunststoffgranulator ist ein wichtiger Bestandteil der Ausrüstung. Ob Produktionsabfälle, Ausschussteile oder Altgeräte – die effiziente Zerkleinerung von Kunststoffen ist entscheidend für die Wiederverwendung, Wiederaufbereitung oder Entsorgung. Allerdings sind nicht alle Granulatoren gleich. Die Auswahl des falsch Maschine kann zu Ineffizienz, schlechter Nachschliffqualität, übermäßigen Ausfallzeiten und letztendlich zu einer geringeren Kapitalrendite (ROI) führen.
Als Experten für Prozessoptimierung wissen wir, wie wichtig die Wahl der richtigen Ausrüstung ist. Dieser Leitfaden befasst sich mit den Wichtige Faktoren, die bei der Auswahl eines Kunststoffgranulators zu berücksichtigen sind, sodass Sie in eine Maschine investieren, die perfekt auf Ihre Betriebsanforderungen abgestimmt ist und Ihren Gewinn steigert.
Ihre Bedürfnisse verstehen: Die Grundlage der Auswahl
Bevor Sie sich in die Maschinenspezifikationen vertiefen, sollten Sie einen Schritt zurücktreten und Ihre Anforderungen klar definieren. Fragen Sie sich:
- Welche konkreten Kunststoffarten werden Sie granulieren? (z. B. PET, HDPE, LDPE, PP, ABS, PC, Nylon? Folie, starr, weich?)
- Welche Form und Größe hat das Eingangsmaterial? (zB kleine Angusskanäle, große Spülungen, Flaschen, Folienrollen, sperrige Teile?)
- Wie hoch ist der erforderliche Durchsatz? (Wie viele Pfund oder Kilogramm müssen Sie pro Stunde verarbeiten?)
- Welche Partikelgröße soll das Endprodukt (Mahlgut) haben? (Muss es für die sofortige Wiederverwendung sehr einheitlich sein oder sind gewisse Abweichungen akzeptabel?)
- Wie passt der Granulator in Ihren bestehenden Arbeitsablauf? (Manuelle Zufuhr, Förderbandzuführung, Roboterintegration?)
Die Beantwortung dieser Fragen bietet eine solide Grundlage für die Bewertung potenzieller Granulatoren.
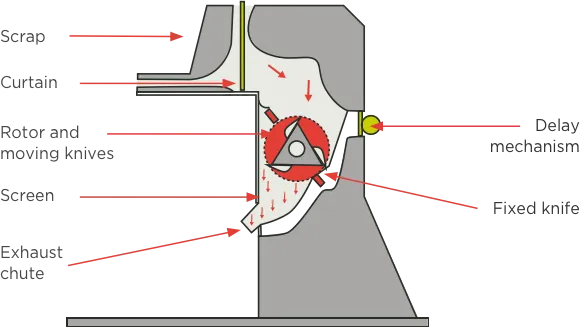
Schlüsselfaktoren für die Auswahl Ihres Kunststoffgranulator
Nachdem wir Ihre Anforderungen definiert haben, untersuchen wir die kritischen technischen und betrieblichen Faktoren:
1. Materialeigenschaften und Anwendung
Dies ist wohl der wichtigste Faktor. Verschiedene Kunststoffe verhalten sich unterschiedlich:
- Harte/spröde Kunststoffe (z. B. Acryl, Polystyrol): Neigen zum Zersplittern. Benötigen robuste Schneidkammern und profitieren oft von einer hohen Scherwirkung (wie V- oder Scherenschnittrotoren).
- Weiche/flexible Kunststoffe (z. B. LDPE-Folie, TPE): Kann sich um Rotoren wickeln oder ist schwer sauber zu schneiden. Oft sind spezielle Rotoren (manchmal offene Rotoren) und scharfe Messer mit spezifischen Winkeln erforderlich. Für Folienanwendungen sind möglicherweise spezielle Zuführsysteme erforderlich.
- Abrasive/gefüllte Kunststoffe (z. B. glasfaserverstärktes Nylon): Verursacht hohen Verschleiß an Messern und Kammern. Erfordert gehärtete Komponenten und einfachen Zugang zum Messer für häufiges Wechseln oder Schärfen.
Einblick: Eine falsche Abstimmung des Granulators auf das Material führt zu schlechtem Mahlgut, Verstopfungen und vorzeitigem Verschleiß. Besprechen Sie Ihre spezifischen Materialien stets mit potenziellen Lieferanten.
2. Durchsatzanforderungen
Ihre erforderliche Verarbeitungsleistung (lbs/h oder kg/h) beeinflusst direkt die Größe und Leistung des benötigten Granulators. Berücksichtigen Sie nicht nur Ihren aktuellen Bedarf, sondern auch potenzielles zukünftiges Wachstum.
Einblick: Unterdimensionierung führt zu Engpässen. Überdimensionierung führt zu unnötigen Investitionen und potenziell höherem Energieverbrauch pro verarbeiteter Materialeinheit. Streben Sie eine Kapazität an, die Ihre Spitzenlast problemlos bewältigt und Spielraum für Wachstum bietet.
3. Erforderliche Mahlgutgröße und -qualität
Die gewünschte Größe und Gleichmäßigkeit des Granulats (Mahlgut) hängt von seiner nächsten Verwendung ab. Die direkte Wiederverwendung neben Neumaterial im Formteil erfordert oft gleichmäßige, kleine Partikelgrößen mit minimalem Feinanteil (Staub).
- Bildschirmgröße: Die Löcher im Sieb des Granulators bestimmen in erster Linie die maximale Partikelgröße. Kleinere Löcher bedeuten kleinere Partikel, aber potenziell einen geringeren Durchsatz.
- Messeraufbau und Schärfe: Durch die gleichmäßige Schneidwirkung wird ein gleichmäßigeres Nachschleifen erreicht.
Einblick: Konsistente, hohe Qualität Mahlgut Verbessert die Weiterverarbeitung und die Qualität des Endprodukts. Geben Sie die gewünschte Partikelgrößenverteilung an.
4. Granulatortyp: Der Standort ist wichtig
- Beistellgranulatoren: Kleiner, direkt neben Verarbeitungsmaschinen (z. B. Spritzgussmaschinen) platziert, um Angusskanäle und Angüsse sofort wiederzugewinnen. Ideal zur Minimierung des Materialhandlings und der Kontamination.
- Zentralgranulatoren: Größere Hochleistungsmaschinen für die Verarbeitung von Schrott aus verschiedenen Quellen oder großen, sperrigen Teilen. Die Beschickung erfolgt üblicherweise über Förderbänder oder Kipper.
- Hochleistungs-/Schredder-Granulator-Systeme: Für sehr große, dicke oder anspruchsvolle Materialien. Oft ist vor der Granulierung ein Vorzerkleinerungsschritt erforderlich.
Einblick: Wählen Sie den Typ, der sich am besten in Ihr Produktionslayout und Ihre Ausschusserzeugungspunkte integrieren lässt. Beistellmühlen bieten sofortige Schrottrückgewinnung, während Zentralgranulatoren größere Mengen verarbeiten.
5. Schneidkammer- und Rotordesign
Das Herzstück des Granulators! Zu den wichtigsten Konstruktionsmerkmalen gehören:
- Offener Rotor: Gut für wärmeempfindliche Materialien oder sperrige, hohle Teile, da es eine bessere Luftzirkulation und Materialaufnahme ermöglicht. Kann bei Filmen manchmal Probleme bereiten.
- Geschlossener (massiver) Rotor: Bietet höhere Trägheit und Festigkeit, geeignet für härtere, dickere Materialien.
- Versetzter Rotor: Die Messer sind versetzt, sodass mehrere Schnitte pro Umdrehung möglich sind. Gute Gesamtleistung.
- V-Cut- oder Scherenschnitt-Rotor: Die abgewinkelten Messer erzeugen eine hochgradige Schneidwirkung. Hervorragend geeignet für saubere Schnitte in zäheren Materialien und gleichmäßiges Mahlgut mit weniger Feinanteil. Ideal für viele technische Kunststoffe.
Einblick: Der Rotordesign hat einen erheblichen Einfluss auf die Schneidleistung, die Nachschliffqualität und die Eignung für bestimmte Materialien. Scherenschnittgranulator liefert bei anspruchsvollen Anwendungen oft hervorragende Ergebnisse.
6. Motorleistung und Antriebssystem
Die Leistung (PS) bzw. Kilowatt (kW) muss ausreichen, um auch schwierigste Materialien und höchste Durchsatzanforderungen ohne Stillstand zu bewältigen. Berücksichtigen Sie das Antriebssystem (z. B. Riemenantrieb, Direktantrieb) hinsichtlich Effizienz und Wartungsaufwand.
Einblick: Angemessen Motorleistung sorgt für einen gleichmäßigen Betrieb und verhindert eine Überlastung oder Beschädigung des Motors.
7. Einfache Reinigung und Wartung
Häufige Materialwechsel erfordern eine schnelle und einfache Reinigung, um Verunreinigungen zu vermeiden. Achten Sie auf:
- Einfacher Zugang zur Schneidkammer und zum Sieb.
- Minimale tote Stellen, in denen sich Material ansammeln kann.
- Schnellverschlussmechanismen für Bildschirme und Paneele.
- Einfache Verfahren zur Messereinstellung und zum Messeraustausch.
Einblick: Ausfallzeiten für Reinigung und Wartung sind kostspielig. Priorisieren Sie Designs, die eine schnelle Abwicklung ermöglichen. Wartungsfreundliche Granulatoren Sparen Sie Zeit und Arbeit.
8. Sicherheitsfunktionen
Nicht verhandelbar. Stellen Sie sicher, dass der Granulator den aktuellen Sicherheitsstandards entspricht, einschließlich:
- Rotor-Sperrmechanismen.
- Sicherheitsverriegelungen an Zugangsplatten und Trichtern.
- Not-Aus-Taster.
- Angemessene Bewachung.
Einblick: Die Sicherheit des Bedieners steht an erster Stelle. Gehen Sie keine Kompromisse ein bei Sicherheitsmerkmale des Granulators.
9. Geräuschpegel
Granulatoren können laut sein. Erwägen Sie schallgedämmte Gehäuse oder geräuscharme Konstruktionen, insbesondere bei Modellen, die neben der Presse in der Nähe von Personal betrieben werden. Beachten Sie die örtlichen Lärmschutzbestimmungen.
Einblick: Geräuscharme Granulatoren Verbessern Sie die Arbeitsumgebung und tragen Sie zur Einhaltung der OSHA- oder anderer gesetzlicher Anforderungen bei.
10. Budget und Gesamtbetriebskosten (TCO)
Obwohl der anfängliche Kaufpreis ein Faktor ist, sollten Sie auch die Gesamtbetriebskosten berücksichtigen:
- Energieverbrauch.
- Kosten für Messerersatz/-schärfung.
- Wartungsarbeiten.
- Mögliche Ausfallkosten.
- Verfügbarkeit und Kosten von Ersatzteilen.
Einblick: Eine billigere Maschine kann auf lange Sicht aufgrund höherer Betriebskosten oder geringerer Zuverlässigkeit mehr kosten. Bewerten Granulator TCO für einen echten Vergleich.
Fazit: Eine fundierte Entscheidung treffen
Die Wahl des richtigen Kunststoffgranulator ist eine wichtige Investition, die sich direkt auf Ihre Betriebseffizienz, Ihre Recyclingbemühungen und Ihre Rentabilität auswirkt. Durch sorgfältige Bewertung Ihrer spezifischen Anforderungen anhand dieser Schlüsselfaktoren – Materialart, Durchsatz, Mahlgutqualität, Granulatortyp, Rotordesign, Leistung, Wartung, Sicherheit, Lärm und Gesamtbetriebskosten – können Sie eine Maschine auswählen, die Ihnen über Jahre hinweg zuverlässige Leistung und maximalen Nutzen bietet.