Warum sich ein Wartungsplan für Granulatoren auszahlt
Ungeplante Ausfallzeiten, schwankende Nachschliffqualität und explodierende Klingenkosten sind auf mangelnde Wartung zurückzuführen. Studien großer OEMs zeigen, dass der Wechsel von einem „Run-to-Failure“-Programm zu einem strukturierten Präventionsprogramm die Ausfallzeiten des Granulators um 65–85 % reduzieren und die Messerlebensdauer verdreifachen kann.
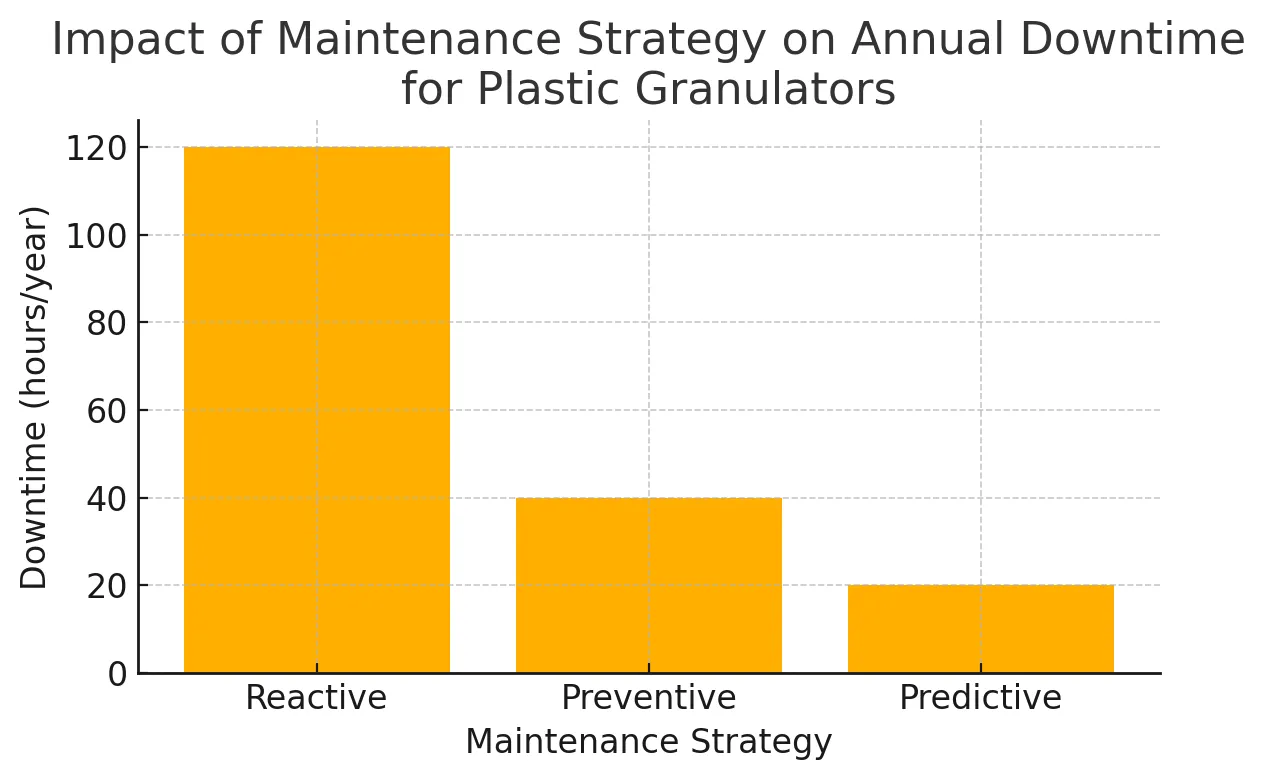
Wichtige Geschäftsvorteile
KPI | Reaktive Wartung | Vorbeugende Wartung | Prädiktiv (sensorbasiert) |
---|---|---|---|
Jährliche Ausfallzeit (Std.)** | 120 | 40 | 20 |
Messerausgaben (US$/t) | $9.50 | $4.20 | $3.10 |
Energieverbrauch (kWh/t) | 98 | 72 | 68 |
**Einen visuellen Vergleich finden Sie im Balkendiagramm unten.
Tägliche Kontrollen – 5 Minuten, die später Stunden sparen
- Visuelle Reinigung – Entfernen Sie Feinanteile rund um den Trichter, die Schneidkammer und das Sieb, um Hitzestau und Blitzbildung zu vermeiden.
- Achten Sie auf Geräusche und Vibrationen – Ein plötzliches Heulen weist häufig auf eine Drift des Messerspalts oder lose Rotorschrauben hin.
- Bildschirmzustand – Ersetzen Sie verstopfte oder verformte Siebe sofort. Schon eine Verstopfung von 10 % kann die Motorlast um 15 % erhöhen.
- Motortemperatur und Ampere – Protokollieren und Trend; Spitzen weisen auf stumpfe Klingen oder Riemenschlupf hin.
- Sicherheitsverriegelungen – Tor- und Trichterschalter bei Schichtbeginn testen.
Wöchentliche/monatliche vorbeugende Aufgaben
Intervall | Aufgabe | Warum es wichtig ist |
---|---|---|
Wöchentlich | Überprüfen Sie die Spannung und den Verschleiß des Antriebsriemens | Lose Riemen verschwenden Energie und beschleunigen den Lagerverschleiß. |
Überprüfen Sie den Abstand zwischen Messer und Bettmesser (typischerweise 0,10–0,25 mm). | Der richtige Abstand bewahrt die scharfe Kante und reduziert Staub. | |
Rotorlager auf Fettentleerung prüfen | Frühes Anzeichen einer Überschmierung oder eines Dichtungsversagens. | |
Monatlich | Lager fetten (OEM-spezifiziertes Fett) | Verhindert Überhitzung und Festfressen. |
Überprüfen Sie das Drehmoment aller Kammerbefestigungen | Beseitigt vibrationsbedingtes Lösen. | |
Überprüfen Sie den Schaltschrank: Klemmen, Leistungsschalter | Eine Verfärbung durch Hitze deutet auf eine Überlastung oder einen schlechten Kontakt hin. |
Klingen- und Siebpflege – Das Herzstück hochwertigen Mahlguts
- Schärfen, bevor die Stumpfheit sichtbar wird. Eine gute Regel: Dünne Folien alle 40–60 Stunden, dicke Teile alle 80–100 Stunden nachschärfen. Klingen können etwa 10 Mal geschärft werden, bevor sie ausgetauscht werden müssen.
- Verwenden Sie eine Präzisionslehre. Um irreversible Rotorschäden zu vermeiden, muss die Teilung nach dem Schleifen den OEM-Spezifikationen entsprechen.
- Sets ausgleichen und kombinieren. Installieren Sie die Messer immer als passende Sätze, um den Rotor im Gleichgewicht zu halten und die Lagerbelastung zu begrenzen.
- Bildschirminventar. Halten Sie pro Maschine zwei Ersatzsiebe bereit. Beschädigte Öffnungen verzerren die Partikelgröße und erhöhen den Feinanteil.
Staub- und Kontaminationskontrolle
Überschüssige Feinteile beeinträchtigen die nachfolgende Extrusion und Injektion. Installieren Sie einen Inline-Entstauber oder Zyklon und leeren Sie die Auffangbehälter täglich. Überprüfen Sie den Absaugluftstrom; ein Abfall von 20 % verdoppelt den Feinteilübertrag.
Motor, Getriebe und Antriebssystem
- Riemenausrichtung. Eine Fehlausrichtung >2 mm halbiert die Lebensdauer des Riemens.
- Probenahme des Getriebeöls. Durch eine vierteljährliche Ölanalyse lässt sich frühzeitig Lochfraß erkennen.
- Sanftanlauf oder VFD. Reduziert Einschaltstrom und mechanische Stöße und verlängert so die Lebensdauer des Motors.
Vorausschauende Wartung
Kostengünstige IoT-Sensoren machen zustandsbasierten Service auch für kleine Anlagen realistisch:
Sensor | Erkennt | Typische Warnung |
---|---|---|
Vibration (IMU) | Lagerverschleiß, Rotorunwucht | RMS-Geschwindigkeit >6 mm/s |
Infrarottemperatur | Motorüberhitzung | >90 °C Statortemperatur |
Stromwandler | Lastspitzen, stumpfe Messer | +15 % über der Grundlinie |
Durch automatisierte Warnmeldungen können die Teams von der Brandbekämpfung auf proaktive Messerwechsel umstellen und so ungeplante Stopps vermeiden.
Arbeitsablauf eines Kunststoffgranulators – Wo Wartung passt
Das oben stehende Bilderkarussell führt durch eine typische Granulierlinie und hebt die Kontrollpunkte (Trichter, Schneidkammer, Siebdeck, Austragsgebläse) hervor. Nutzen Sie es als visuelle Hilfe bei der Schulung von Bedienern.
Auswirkungen der Wartungsstrategie auf die Leistung
Das folgende Diagramm veranschaulicht, wie die Ausfallzeiten sinken, wenn Sie von reaktiver auf vorausschauende Wartung umsteigen.
(Diagramm oben angezeigt)
Nutzen Sie das Ausfallzeitdelta, um Ihren ROI-Fall aufzubauen: Jede Stunde, die ein 75-kW-Granulator stillsteht, kostet ≈ US$180 an verlorenem Durchsatz und Arbeitsaufwand.
Erstellen Sie Ihren eigenen Wartungsplan
- Beginnen Sie mit den OEM-Empfehlungen und passen Sie es an Ihren Materialmix an (abrasives glasfaserverstärktes PP vs. weiches LDPE).
- Alles protokollieren – Messerstunden, Siebwechsel, Bandwechsel. Eine einfache Tabellenkalkulation oder ein CMMS reicht aus.
- Bediener schulen und befähigen. 80 % der Ausfälle weisen frühe Symptome auf, die vom Produktionspersonal erkannt werden können.
- Bewahren Sie wichtige Ersatzteile auf. Minimum: kompletter Messersatz, zwei Siebe, Antriebsriemensatz, Fett, Hauptlager.
Sicherheit geht vor
Beachten Sie vor dem Betreten der Schneidkammer stets die Lock-out/Tag-out-Vorschriften (LOTO). Stellen Sie sicher, dass keine gespeicherte Energie vorhanden ist – Riemen, Schwungräder und Hydraulikdeckel können auch bei ausgeschalteter Stromversorgung ihre Kraft behalten.
Fazit – Fünf Erkenntnisse
- Ein dokumentierter Präventionsplan verkürzt die Ausfallzeit um >60 %.
- Scharfe Messer mit dem richtigen Abstand steigern Ihren Durchsatz am günstigsten.
- Die Inspektion von Riemen, Lagern und Sieben dauert nur wenige Minuten, Vernachlässigung kostet Tage.
- Staubkontrolle und Motorlastoptimierung verbessern sowohl die Produktqualität als auch den Energieverbrauch.
- Technologien zur vorausschauenden Wartung sind jetzt erschwinglich – beginnen Sie im Kleinen mit Vibrationssensoren.
Durch die Integration dieser Verfahren stellen Einkäufer und technische Teams sicher, dass ihre Investitionen in Granulatoren eine gleichbleibende Mahlgutqualität, geringere Betriebskosten und maximale Betriebszeit gewährleisten.