In the world of plastics processing and recycling, the granulador de plástico is a cornerstone piece of equipment. Whether you’re dealing with production scrap, rejected parts, or post-consumer waste, efficiently reducing plastic size is crucial for reuse, reprocessing, or disposal. However, not all granulators are created equal. Selecting the wrong machine can lead to inefficiency, poor regrind quality, excessive downtime, and ultimately, a lower return on investment (ROI).
As experts in optimizing processes, we understand that making the right equipment choice is vital. This guide delves into the key factors to consider when choosing a plastic granulator, ensuring you invest in a machine that perfectly aligns with your operational needs and enhances your bottom line.
Understanding Your Needs: The Foundation of Selection
Before diving into machine specifications, take a step back and clearly define your requirements. Ask yourself:
- What specific types of plastic will you be granulating? (e.g., PET, HDPE, LDPE, PP, ABS, PC, Nylon? Film, rigid, soft?)
- What is the form and size of the input material? (e.g., small runners, large purgings, bottles, film rolls, bulky parts?)
- What is the required throughput? (How many pounds or kilograms per hour do you need to process?)
- What is the desired output particle size (regrind)? (Does it need to be highly uniform for immediate reuse, or is some variation acceptable?)
- How will the granulator fit into your existing workflow? (Manual feed, conveyor feed, robotic integration?)
Answering these questions provides a solid foundation for evaluating potential granulators.
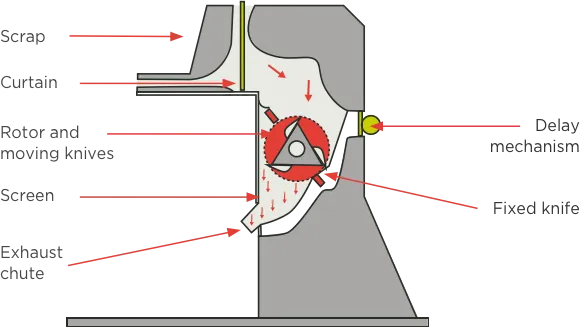
Key Factors for Choosing Your Granulador de plástico
With your needs defined, let’s explore the critical technical and operational factors:
1. Material Characteristics & Application
This is arguably the most crucial factor. Different plastics behave differently:
- Hard/Brittle Plastics (e.g., Acrylic, Polystyrene): Tend to shatter. Require robust cutting chambers and often benefit from high shear cutting action (like V-cut or scissor-cut rotors).
- Soft/Flexible Plastics (e.g., LDPE Film, TPE): Can wrap around rotors or be difficult to cut cleanly. Often require specialized rotors (sometimes open rotors) and sharp knives with specific angles. Film applications may need specific feeding systems.
- Abrasive/Filled Plastics (e.g., Glass-Filled Nylon): Cause high wear on knives and chambers. Require hardened components and easy knife access for frequent changes or sharpening.
Insight: Mismatching the granulator to the material leads to poor regrind, jams, and premature wear. Always discuss your specific materials with potential suppliers.
2. Throughput Requirements
Your required processing rate (lbs/hr or kg/hr) directly influences the size and power of the granulator needed. Don’t just consider your current needs; think about potential future growth.
Insight: Undersizing leads to bottlenecks. Oversizing leads to unnecessary capital expenditure and potentially higher energy consumption per unit of material processed. Aim for a capacity that comfortably handles your peak load with some room for growth.
3. Required Regrind Size and Quality
The desired size and uniformity of the granulated material (regrind) depend on its next use. Direct reuse alongside virgin material in molding often requires consistent, small particle sizes with minimal fines (dust).
- Tamaño de pantalla: The holes in the granulator’s screen primarily determine the maximum particle size. Smaller holes = smaller particles, but potentially lower throughput.
- Knife Setup & Sharpness: Consistent cutting action produces more uniform regrind.
Insight: Consistent, high-quality regrind improves downstream processing and final product quality. Specify your required particle size distribution.
4. Granulator Type: Location Matters
- Beside-the-Press Granulators: Smaller, placed directly next to processing machines (e.g., injection molders) to immediately reclaim runners and sprues. Ideal for minimizing material handling and contamination.
- Central Granulators: Larger, heavy-duty machines designed to handle scrap from multiple sources or large, bulky parts. Typically fed via conveyors or dumpers.
- Heavy-Duty / Shredder-Granulator Systems: For very large, thick, or challenging materials. Often involve a pre-shredding step before granulation.
Insight: Choose the type that best integrates with your production layout and scrap generation points. Beside-the-press granulators offer immediate scrap recovery, while central granulators handle larger volumes.
5. Cutting Chamber and Rotor Design
The heart of the granulator! Key designs include:
- Open Rotor: Good for heat-sensitive materials or bulky, hollow parts as it allows better airflow and material ingestion. Can sometimes struggle with film.
- Closed (Solid) Rotor: Offers higher inertia and strength, suitable for harder, thicker materials.
- Staggered Rotor: Knives are offset, providing multiple bites per revolution. Good all-around performance.
- V-Cut or Scissor-Cut Rotor: Knives are angled, creating a high-shear cutting action. Excellent for achieving clean cuts on tougher materials and producing uniform regrind with fewer fines. Ideal for many technical plastics.
Insight: El rotor design significantly impacts cutting efficiency, regrind quality, and suitability for specific materials. A scissor-cut granulator often provides superior results for demanding applications.
6. Motor Power and Drive System
Horsepower (HP) or Kilowatts (kW) must be sufficient to handle the toughest materials and highest throughput demands without stalling. Consider the drive system (e.g., belt drive, direct drive) for efficiency and maintenance implications.
Insight: Adequate motor power ensures consistent operation and prevents motor overload or damage.
7. Ease of Cleaning and Maintenance
Frequent material changes require quick and easy cleaning to prevent contamination. Look for:
- Easy access to the cutting chamber and screen.
- Minimal dead spots where material can accumulate.
- Quick-release mechanisms for screens and panels.
- Simple knife adjustment and replacement procedures.
Insight: Downtime for cleaning and maintenance is costly. Prioritize designs that facilitate quick turnaround. Easy maintenance granulators save time and labor.
8. Safety Features
Non-negotiable. Ensure the granulator meets current safety standards, including:
- Rotor lock-out mechanisms.
- Safety interlocks on access panels and hoppers.
- Emergency stop buttons.
- Appropriate guarding.
Insight: Operator safety is paramount. Never compromise on granulator safety features.
9. Noise Level
Granulators can be noisy. Consider soundproofed enclosures or low-noise designs, especially for beside-the-press models operating near personnel. Check local noise regulations.
Insight: Low-noise granulators improve the working environment and help meet OSHA or other regulatory requirements.
10. Budget and Total Cost of Ownership (TCO)
While the initial purchase price is a factor, consider the TCO:
- Energy consumption.
- Knife replacement/sharpening costs.
- Maintenance labor.
- Potential downtime costs.
- Spare parts availability and cost.
Insight: A cheaper machine might cost more in the long run due to higher operating expenses or lower reliability. Evaluate granulator TCO for a true comparison.
Conclusion: Making an Informed Decision
Elegir lo correcto granulador de plástico is a critical investment that directly impacts your operational efficiency, recycling efforts, and profitability. By carefully evaluating your specific needs against these key factors – material type, throughput, regrind quality, granulator type, rotor design, power, maintenance, safety, noise, and TCO – you can select a machine that delivers reliable performance and maximum value for years to come.