Dans le monde de la transformation et du recyclage des plastiques, granulateur de plastique est un équipement essentiel. Qu'il s'agisse de rebuts de production, de pièces rejetées ou de déchets post-consommation, la réduction efficace de la taille du plastique est essentielle pour sa réutilisation, son retraitement ou son élimination. Cependant, tous les granulateurs ne se valent pas. Choisir le faux La machine peut entraîner une inefficacité, une mauvaise qualité de broyage, des temps d'arrêt excessifs et, en fin de compte, un retour sur investissement (ROI) plus faible.
En tant qu'experts en optimisation des processus, nous comprenons l'importance de choisir le bon équipement. Ce guide explore les facteurs clés à prendre en compte lors du choix d'un granulateur de plastique, vous assurant d'investir dans une machine qui s'adapte parfaitement à vos besoins opérationnels et améliore vos résultats.
Comprendre vos besoins : le fondement de la sélection
Avant de vous plonger dans les spécifications de votre machine, prenez du recul et définissez clairement vos besoins. Posez-vous les questions suivantes :
- Quels types spécifiques de plastique allez-vous granuler ? (par exemple, PET, HDPE, LDPE, PP, ABS, PC, Nylon ? Film, rigide, souple ?)
- Quelle est la forme et la taille du matériau d'entrée ? (par exemple, petits coureurs, grandes purges, bouteilles, rouleaux de film, pièces volumineuses ?)
- Quel est le débit requis ? (Combien de livres ou de kilogrammes par heure devez-vous traiter ?)
- Quelle est la granulométrie de sortie souhaitée (rebroyé) ? (Devrait-il être très uniforme pour une réutilisation immédiate, ou une certaine variation est-elle acceptable ?)
- Comment le granulateur s'intégrera-t-il dans votre flux de travail existant ? (Alimentation manuelle, alimentation par convoyeur, intégration robotisée ?)
Répondre à ces questions fournit une base solide pour évaluer les granulateurs potentiels.
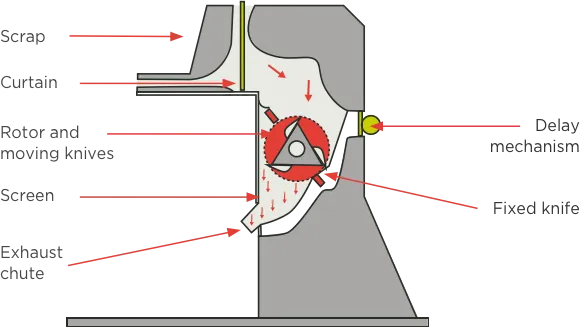
Facteurs clés pour choisir votre Granulateur de plastique
Une fois vos besoins définis, explorons les facteurs techniques et opérationnels critiques :
1. Caractéristiques du matériau et application
C'est sans doute le facteur le plus crucial. Les différents plastiques se comportent différemment :
- Plastiques durs/cassants (par exemple, acrylique, polystyrène) : Tendance à se briser. Nécessite des chambres de coupe robustes et bénéficie souvent d'une action de coupe à cisaillement élevé (comme les rotors à coupe en V ou en ciseaux).
- Plastiques souples/flexibles (par exemple, film LDPE, TPE) : Peut s'enrouler autour des rotors ou être difficile à couper proprement. Nécessite souvent des rotors spécialisés (parfois ouverts) et des couteaux tranchants avec des angles spécifiques. Les applications de films peuvent nécessiter des systèmes d'alimentation spécifiques.
- Plastiques abrasifs/chargés (par exemple, nylon chargé de verre) : Provoque une usure importante des couteaux et des chambres. Nécessite des composants renforcés et un accès facile aux couteaux pour des changements ou des affûtages fréquents.
Aperçu: Une mauvaise adaptation du granulateur au matériau peut entraîner un rebroyage de mauvaise qualité, des bourrages et une usure prématurée. Discutez toujours de vos matériaux spécifiques avec vos fournisseurs potentiels.
2. Exigences de débit
Votre débit de traitement requis (lb/h ou kg/h) influence directement la taille et la puissance du granulateur nécessaire. Ne vous limitez pas à vos besoins actuels ; pensez également à votre potentiel de croissance future.
Aperçu: Un sous-dimensionnement entraîne des goulots d'étranglement. Un surdimensionnement entraîne des dépenses d'investissement inutiles et une consommation d'énergie potentiellement plus élevée par unité de matière traitée. Visez une capacité capable de gérer confortablement vos pics de charge, avec une marge de croissance.
3. Taille et qualité du rebroyé requises
La granulométrie et l'uniformité souhaitées du matériau granulé (rebroyé) dépendent de son utilisation ultérieure. Une réutilisation directe avec du matériau vierge dans le moulage nécessite souvent des particules de petite taille et homogènes, avec un minimum de fines (poussières).
- Taille de l'écran : Les trous du tamis du granulateur déterminent principalement la taille maximale des particules. Plus les trous sont petits, plus les particules sont petites, mais le débit peut être plus faible.
- Configuration et tranchant du couteau : Une action de coupe uniforme produit un broyage plus uniforme.
Aperçu: Cohérent et de haute qualité broyé Améliore le traitement en aval et la qualité du produit final. Précisez la granulométrie souhaitée.
4. Type de granulateur : l'emplacement est important
- Granulateurs à côté de la presse : Plus petit, il est placé directement à côté des machines de traitement (par exemple, les presses à injecter) pour récupérer immédiatement les canaux et les carottes. Idéal pour minimiser la manutention et la contamination des matériaux.
- Granulateurs centraux : Machines plus grandes et robustes, conçues pour traiter des déchets provenant de sources multiples ou des pièces volumineuses et encombrantes. Généralement alimentées par des convoyeurs ou des basculeurs.
- Systèmes de broyage-granulation à usage intensif : Pour les matériaux très volumineux, épais ou difficiles à traiter. Nécessite souvent une étape de pré-broyage avant la granulation.
Aperçu: Choisissez le type qui s'intègre le mieux à votre configuration de production et à vos points de génération de rebuts. Granulateurs à côté de la presse offrent une récupération immédiate des déchets, tout en granulateurs centraux gérer des volumes plus importants.
5. Conception de la chambre de coupe et du rotor
Le cœur du granulateur ! Parmi ses principales caractéristiques :
- Rotor ouvert : Idéal pour les matériaux thermosensibles ou les pièces volumineuses et creuses, car il permet une meilleure circulation de l'air et une meilleure absorption du matériau. Peut parfois poser problème avec le film.
- Rotor fermé (solide) : Offre une inertie et une résistance supérieures, adapté aux matériaux plus durs et plus épais.
- Rotor décalé : Les couteaux sont décalés, permettant plusieurs morsures par tour. Excellentes performances générales.
- Rotor à coupe en V ou en ciseaux : Les couteaux sont inclinés, créant une coupe à fort cisaillement. Ils sont parfaits pour des coupes nettes sur des matériaux plus résistants et pour un broyage uniforme avec moins de fines particules. Idéal pour de nombreux plastiques techniques.
Aperçu: Le conception du rotor impacte considérablement l'efficacité de coupe, la qualité du broyage et l'adéquation à des matériaux spécifiques. granulateur à coupe en ciseaux fournit souvent des résultats supérieurs pour les applications exigeantes.
6. Système d'alimentation et d'entraînement du moteur
La puissance (CV) ou les kilowatts (kW) doivent être suffisants pour traiter les matériaux les plus résistants et les débits les plus élevés sans caler. Tenez compte du système d'entraînement (par exemple, entraînement par courroie, entraînement direct) pour en évaluer l'efficacité et les implications en termes de maintenance.
Aperçu: Adéquat puissance du moteur assure un fonctionnement constant et évite la surcharge ou les dommages du moteur.
7. Facilité de nettoyage et d'entretien
Les changements fréquents de matériaux nécessitent un nettoyage rapide et facile pour éviter toute contamination. Recherchez :
- Accès facile à la chambre de coupe et à l'écran.
- Points morts minimes où le matériau peut s'accumuler.
- Mécanismes de dégagement rapide pour écrans et panneaux.
- Procédures simples de réglage et de remplacement des couteaux.
Aperçu: Les temps d'arrêt pour le nettoyage et la maintenance sont coûteux. Privilégiez les conceptions qui permettent une intervention rapide. Granulateurs faciles d'entretien gagner du temps et du travail.
8. Caractéristiques de sécurité
Non négociable. Assurez-vous que le granulateur est conforme aux normes de sécurité en vigueur, notamment :
- Mécanismes de verrouillage du rotor.
- Verrouillages de sécurité sur les panneaux d'accès et les trémies.
- Boutons d'arrêt d'urgence.
- Garde appropriée.
Aperçu: La sécurité de l'opérateur est primordiale. Ne faites jamais de compromis sur caractéristiques de sécurité du granulateur.
9. Niveau sonore
Les granulateurs peuvent être bruyants. Envisagez des enceintes insonorisées ou des conceptions silencieuses, notamment pour les modèles situés à côté de la presse et fonctionnant à proximité du personnel. Consultez la réglementation locale en matière de bruit.
Aperçu: Granulateurs à faible bruit améliorer l’environnement de travail et contribuer à répondre aux exigences de l’OSHA ou d’autres exigences réglementaires.
10. Budget et coût total de possession (TCO)
Bien que le prix d’achat initial soit un facteur, tenez compte du coût total de possession :
- Consommation d'énergie.
- Coûts de remplacement/affûtage des couteaux.
- Main d'oeuvre d'entretien.
- Coûts potentiels liés aux temps d’arrêt.
- Disponibilité et coût des pièces de rechange.
Aperçu: Une machine moins chère peut coûter plus cher à long terme en raison de frais d'exploitation plus élevés ou d'une fiabilité moindre. granulateur TCO pour une véritable comparaison.
Conclusion : Prendre une décision éclairée
Choisir le bon granulateur de plastique Il s'agit d'un investissement crucial qui impacte directement votre efficacité opérationnelle, vos efforts de recyclage et votre rentabilité. En évaluant soigneusement vos besoins spécifiques en fonction de ces facteurs clés (type de matériau, débit, qualité du rebroyé, type de granulateur, conception du rotor, puissance, maintenance, sécurité, bruit et coût total de possession), vous pouvez choisir une machine offrant des performances fiables et une valeur optimale pour les années à venir.