Plastic granulator is at the core of recycling and manufacturing, transforming bulky plastic waste into manageable, reusable regrind. But at the heart of this essential process is a crucial component often underestimated: the plastic granulator cutter. Selecting an inappropriate cutter can lead to reduced efficiency, poor-quality regrind, higher energy use, frequent downtime, and elevated operational costs.
On the other hand, choosing the correct granulator knives or pelletizer blades can significantly boost efficiency, enhance regrind quality, extend machinery lifespan, and substantially lower costs. This comprehensive guide explains how to select the ideal plastic granulator cutter to fit your specific application.
Why Choosing the Right Granulator Cutter Matters
Think of granulator cutters as the teeth of your recycling operation, directly impacting:
- Throughput & Efficiency: Sharp, appropriate blades quickly process materials, maximizing output.
- Regrind Quality: Correct blades ensure uniform particle sizes and reduce fines (dust), crucial for consistent downstream processing.
- Potrošnja energije: Dull or incorrect blades increase energy use, driving up operational costs.
- Maintenance & Downtime: Durable blades reduce maintenance frequency and downtime, saving significant costs.
- Overall Operating Costs: Efficient blades directly lower your operational expenses per pound/kilo of material processed.
Understanding Granulator Cutter Types
Most granulators use two main types of cutters:
- Rotor Knives (Fly Knives): Mounted on the spinning rotor, they perform primary cutting.
- Stator Knives (Bed Knives): Fixed knives providing a stationary counter-edge for shearing action.
The interaction, alignment, and sharpness of these knives are critical for optimal granulation.
Key Factors for Selecting Your Ideal Granulator Cutter
Selecting the perfect cutter depends on several critical factors:
1. Material Being Processed
The material type greatly influences blade selection:
- Soft & Flexible Plastics (LDPE films, PP fibers): Require sharp angles and coatings to avoid wrapping, favoring a scissor-cut, high-shear action.
- Hard & Brittle Plastics (ABS, HIPS, PC): Need robust, impact-resistant blades with lower shear angles.
- Abrasive or Filled Plastics (Glass-filled Nylon, Talc-filled PP): Demand wear-resistant materials (e.g., tungsten carbide inserts) and surface coatings (TiN, CrN).
- Contaminated Materials: Impact-resistant blades handle occasional foreign objects better.
2. Desired Particle Size and Quality
Your final regrind specifications directly influence cutter choice:
- Uniformity: Precise cutter geometry and sharpness are critical.
- Reduced Fines: Cleaner shearing cuts produce fewer fines.
- Screen Compatibility: Ensure cutters effectively reduce materials to desired screen size.
3. Granulator Size and Design
Match cutters to your granulator:
- Rotor Type (Open vs. Closed): Open rotors suit heat-sensitive or bulky materials, closed rotors manage tougher plastics.
- Cutting Chamber Geometry: Consider rotor designs—V-cut, stagger-cut, straight-cut—each optimized for different applications.
- Machine Compatibility: Confirm dimensional correctness (bolt patterns, thickness).
4. Cutter Material and Hardness
Blade materials affect durability, wear resistance, and costs:
- Standard Tool Steel (D2): Good for general purposes, cost-effective but wears quicker with abrasive materials.
- High-Alloy Tool Steels (CPM grades): Superior wear resistance and toughness for demanding applications.
- Tungsten Carbide: Exceptional wear resistance, ideal for abrasive plastics, albeit costlier and more brittle.
- Surface Coatings (TiN, CrN): Enhance hardness and lubricity, significantly extending cutter life.
High-performance blades cost more initially but reduce total ownership costs due to less downtime and replacements.
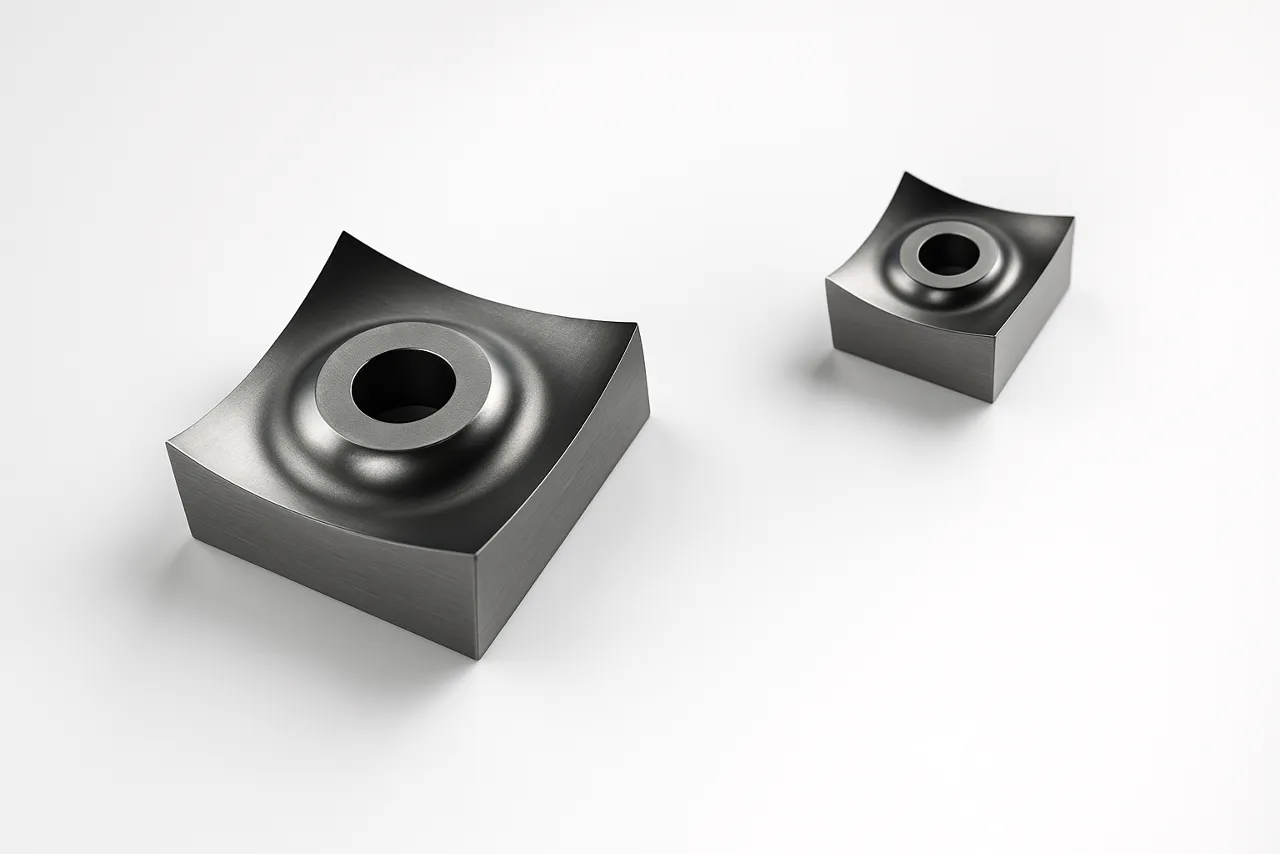
5. Cutter Geometry and Cutting Angle
Blade geometry impacts cutting performance:
- Shear Angle: High shear angles provide cleaner cuts suitable for soft plastics; low angles provide impact force for harder plastics.
- Hook Angle: Influences how aggressively blades pull material into the cut.
- Multiple Cutting Edges: Extend life by allowing rotation of cutting edges before sharpening or replacement.
Linking Cutter Choice to Efficiency and Cost Reduction
Proper cutter selection optimizes costs and productivity through:
- Smanjeno vrijeme prekida rada: Durable blades minimize blade changes or sharpening needs.
- Lower Energy Consumption: Sharp, optimized blades reduce strain on motors.
- Enhanced Regrind Quality: Uniform particle sizes boost downstream processing efficiency and product value.
- Longer Machine Lifespan: Efficient cutting minimizes mechanical wear.
- Optimized Throughput: Matching blades to materials maximizes operational capacity.
- Cost-Effective Blade Management: Higher quality blades, though initially pricier, reduce long-term replacement frequency.
Maximizing Cutter Lifespan with Maintenance
Maintain blades effectively:
- Regular Inspection: Check for dullness, chips, or damage.
- Proper Sharpening: Follow correct techniques to restore blade edges safely.
- Knife Gap Accuracy: Maintain proper clearance between rotor and stator knives.
- Routine Cleaning: Keep cutting chambers free of material buildup.
Conclusion: Strategic Investment in Granulator Cutters
Odabir pravog plastični granulator cutter is more than routine maintenance—it’s a strategic decision that significantly affects your operational efficiency and profitability. By carefully evaluating your materials, required regrind quality, granulator specifications, and blade options, you’ll unlock substantial performance improvements and cost savings.
Avoid generic choices. Evaluate your specific needs carefully, seek professional guidance if necessary, and invest in granulator cutters that optimize performance, durability, and overall cost-effectiveness. The result: a smoother, faster, and more profitable plastic granulation process.