Nel mondo della lavorazione e del riciclaggio delle materie plastiche, granulatore di plastica è un elemento fondamentale dell'attrezzatura. Che tu abbia a che fare con scarti di produzione, parti scartate o rifiuti post-consumo, ridurre in modo efficiente le dimensioni della plastica è fondamentale per il riutilizzo, la rielaborazione o lo smaltimento. Tuttavia, non tutti i granulatori sono creati uguali. Selezione del sbagliato macchina può portare a inefficienza, scarsa qualità della macinatura, tempi di fermo eccessivi e, in ultima analisi, un ritorno sull'investimento (ROI) inferiore.
In quanto esperti nell'ottimizzazione dei processi, sappiamo che fare la scelta giusta dell'attrezzatura è fondamentale. Questa guida approfondisce fattori chiave da considerare quando si sceglie un granulatore di plastica, assicurandoti di investire in una macchina che si adatta perfettamente alle tue esigenze operative e migliora i tuoi profitti.
Comprendere le tue esigenze: il fondamento della selezione
Prima di immergerti nelle specifiche della macchina, fai un passo indietro e definisci chiaramente i tuoi requisiti. Chiediti:
- Quali tipi specifici di plastica verranno granulati? (ad esempio, PET, HDPE, LDPE, PP, ABS, PC, Nylon? Pellicola, rigida, morbida?)
- Qual è la forma e la dimensione del materiale in ingresso? (ad esempio, piccoli canali di colata, grandi spurghi, bottiglie, rulli di pellicola, parti ingombranti?)
- Qual è la portata richiesta? (Quante libbre o chilogrammi all'ora devi elaborare?)
- Qual è la dimensione desiderata delle particelle in uscita (rimacinato)? (Deve essere estremamente uniforme per un riutilizzo immediato oppure sono accettabili alcune variazioni?)
- Come si adatterà il granulatore al tuo flusso di lavoro attuale? (Alimentazione manuale, alimentazione tramite trasportatore, integrazione robotica?)
Rispondere a queste domande fornisce una solida base per la valutazione dei potenziali granulatori.
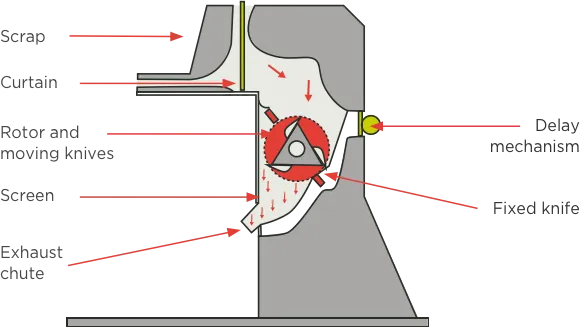
Fattori chiave per la scelta del tuo Granulatore di plastica
Una volta definite le tue esigenze, esploriamo i fattori tecnici e operativi critici:
1. Caratteristiche del materiale e applicazione
Questo è probabilmente il fattore più cruciale. Le diverse plastiche si comportano in modo diverso:
- Plastiche dure/fragili (ad esempio, acrilico, polistirene): Tendono a rompersi. Richiedono camere di taglio robuste e spesso beneficiano di un'azione di taglio ad alta cesoia (come i rotori a V o a forbice).
- Plastiche morbide/flessibili (ad esempio, film LDPE, TPE): Può avvolgersi attorno ai rotori o essere difficile da tagliare in modo netto. Spesso richiede rotori specializzati (a volte rotori aperti) e coltelli affilati con angoli specifici. Le applicazioni di film potrebbero richiedere sistemi di alimentazione specifici.
- Plastica abrasiva/riempita (ad esempio nylon caricato con fibra di vetro): Causano un'elevata usura di coltelli e camere. Richiedono componenti temprati e un facile accesso ai coltelli per frequenti cambi o affilatura.
Intuizione: L'errato abbinamento del granulatore al materiale porta a una scarsa macinatura, inceppamenti e usura prematura. Discuti sempre dei tuoi materiali specifici con i potenziali fornitori.
2. Requisiti di produttività
La velocità di lavorazione richiesta (lbs/hr o kg/hr) influenza direttamente le dimensioni e la potenza del granulatore necessario. Non considerare solo le tue esigenze attuali; pensa alla potenziale crescita futura.
Intuizione: Il sottodimensionamento porta a colli di bottiglia. Il sovradimensionamento porta a spese di capitale non necessarie e a un consumo energetico potenzialmente più elevato per unità di materiale lavorato. Punta a una capacità che gestisca comodamente il tuo carico di picco con un certo margine di crescita.
3. Dimensioni e qualità richieste del macinato
La dimensione desiderata e l'uniformità del materiale granulare (rimacinato) dipendono dal suo utilizzo successivo. Il riutilizzo diretto insieme al materiale vergine nello stampaggio richiede spesso dimensioni delle particelle piccole e costanti con una minima quantità di polvere fine.
- Dimensioni dello schermo: I fori nello schermo del granulatore determinano principalmente la dimensione massima delle particelle. Fori più piccoli = particelle più piccole, ma potenzialmente una produttività inferiore.
- Impostazione e affilatura del coltello: Un'azione di taglio costante produce una macinatura più uniforme.
Intuizione: Coerente, di alta qualità rimacinare migliora la lavorazione a valle e la qualità del prodotto finale. Specifica la distribuzione dimensionale delle particelle richiesta.
4. Tipo di granulatore: la posizione è importante
- Granulatori a bordo pressa: Più piccolo, posizionato direttamente accanto alle macchine di lavorazione (ad esempio, macchine per stampaggio a iniezione) per recuperare immediatamente canali di colata e sprue. Ideale per ridurre al minimo la manipolazione e la contaminazione dei materiali.
- Granulatori Centrali: Macchine più grandi e pesanti, progettate per gestire rottami provenienti da più fonti o parti grandi e ingombranti. Solitamente alimentate tramite nastri trasportatori o dumper.
- Sistemi per impieghi gravosi / trituratori-granulatori: Per materiali molto grandi, spessi o difficili. Spesso comportano una fase di pre-triturazione prima della granulazione.
Intuizione: Scegli la tipologia che meglio si integra con il tuo layout di produzione e con i punti di generazione degli scarti. Granulatori a bordo pressa offrire un recupero immediato degli scarti, mentre granulatori centrali gestire volumi maggiori.
5. Progettazione della camera di taglio e del rotore
Il cuore del granulatore! I progetti chiave includono:
- Rotore aperto: Ottimo per materiali sensibili al calore o parti ingombranti e cave, in quanto consente un migliore flusso d'aria e un'aspirazione migliore del materiale. A volte può avere difficoltà con la pellicola.
- Rotore chiuso (solido): Offre maggiore inerzia e resistenza, adatto ai materiali più duri e spessi.
- Rotore sfalsato: I coltelli sono sfalsati, offrendo più morsi per rivoluzione. Buone prestazioni generali.
- Rotore con taglio a V o a forbice: I coltelli sono angolati, creando un'azione di taglio ad alto taglio. Eccellenti per ottenere tagli puliti su materiali più duri e produrre una riaffilatura uniforme con meno fini. Ideali per molte plastiche tecniche.
Intuizione: IL progettazione del rotore influisce in modo significativo sull'efficienza di taglio, sulla qualità della riaffilatura e sull'idoneità per materiali specifici. A granulatore a forbice spesso fornisce risultati superiori per le applicazioni più impegnative.
6. Potenza del motore e sistema di azionamento
La potenza (HP) o i kilowatt (kW) devono essere sufficienti per gestire i materiali più difficili e le richieste di produttività più elevate senza stalli. Considerare il sistema di trasmissione (ad esempio, trasmissione a cinghia, trasmissione diretta) per le implicazioni di efficienza e manutenzione.
Intuizione: Adeguato potenza del motore garantisce un funzionamento costante e previene sovraccarichi o danni al motore.
7. Facilità di pulizia e manutenzione
I frequenti cambi di materiale richiedono una pulizia rapida e semplice per prevenire la contaminazione. Cerca:
- Facile accesso alla camera di taglio e allo schermo.
- Punti morti minimi in cui il materiale può accumularsi.
- Meccanismi di sgancio rapido per schermi e pannelli.
- Semplici procedure di regolazione e sostituzione dei coltelli.
Intuizione: I tempi di inattività per la pulizia e la manutenzione sono costosi. Dai priorità a progetti che facilitino un rapido turnaround. Granulatori di facile manutenzione risparmiare tempo e fatica.
8. Caratteristiche di sicurezza
Non negoziabile. Assicurarsi che il granulatore soddisfi gli standard di sicurezza correnti, tra cui:
- Meccanismi di blocco del rotore.
- Interblocchi di sicurezza su pannelli di accesso e tramogge.
- Pulsanti di arresto di emergenza.
- Protezione adeguata.
Intuizione: La sicurezza dell'operatore è fondamentale. Non scendere mai a compromessi caratteristiche di sicurezza del granulatore.
9. Livello di rumore
I granulatori possono essere rumorosi. Considerare involucri insonorizzati o progetti a basso rumore, specialmente per i modelli da affiancare alla pressa che operano vicino al personale. Verificare le normative locali sul rumore.
Intuizione: Granulatori a bassa rumorosità migliorare l'ambiente di lavoro e contribuire a soddisfare i requisiti OSHA o altri requisiti normativi.
10. Budget e costo totale di proprietà (TCO)
Sebbene il prezzo di acquisto iniziale sia un fattore, bisogna considerare il TCO:
- Consumo energetico.
- Costi di sostituzione/affilatura dei coltelli.
- Manodopera di manutenzione.
- Potenziali costi di inattività.
- Disponibilità e costo dei pezzi di ricambio.
Intuizione: Una macchina più economica potrebbe costare di più a lungo termine a causa di maggiori spese operative o minore affidabilità. Valutare granulatore TCO per un confronto veritiero.
Conclusione: prendere una decisione informata
Scegliere il giusto granulatore di plastica è un investimento critico che ha un impatto diretto sulla tua efficienza operativa, sugli sforzi di riciclaggio e sulla redditività. Valutando attentamente le tue esigenze specifiche rispetto a questi fattori chiave (tipo di materiale, produttività, qualità di rimacinazione, tipo di granulatore, design del rotore, potenza, manutenzione, sicurezza, rumore e TCO), puoi selezionare una macchina che offre prestazioni affidabili e il massimo valore per gli anni a venire.