Por que um plano de manutenção de granulador rende dividendos
Paradas não programadas, qualidade inconsistente da retificação e custos crescentes das lâminas são fatores que contribuem para a má manutenção. Estudos realizados por grandes fabricantes de equipamentos originais (OEMs) mostram que a transição de um programa de "operação até a falha" para um programa preventivo estruturado pode reduzir o tempo de parada do granulador em 65 a 85 % e triplicar a vida útil da lâmina.
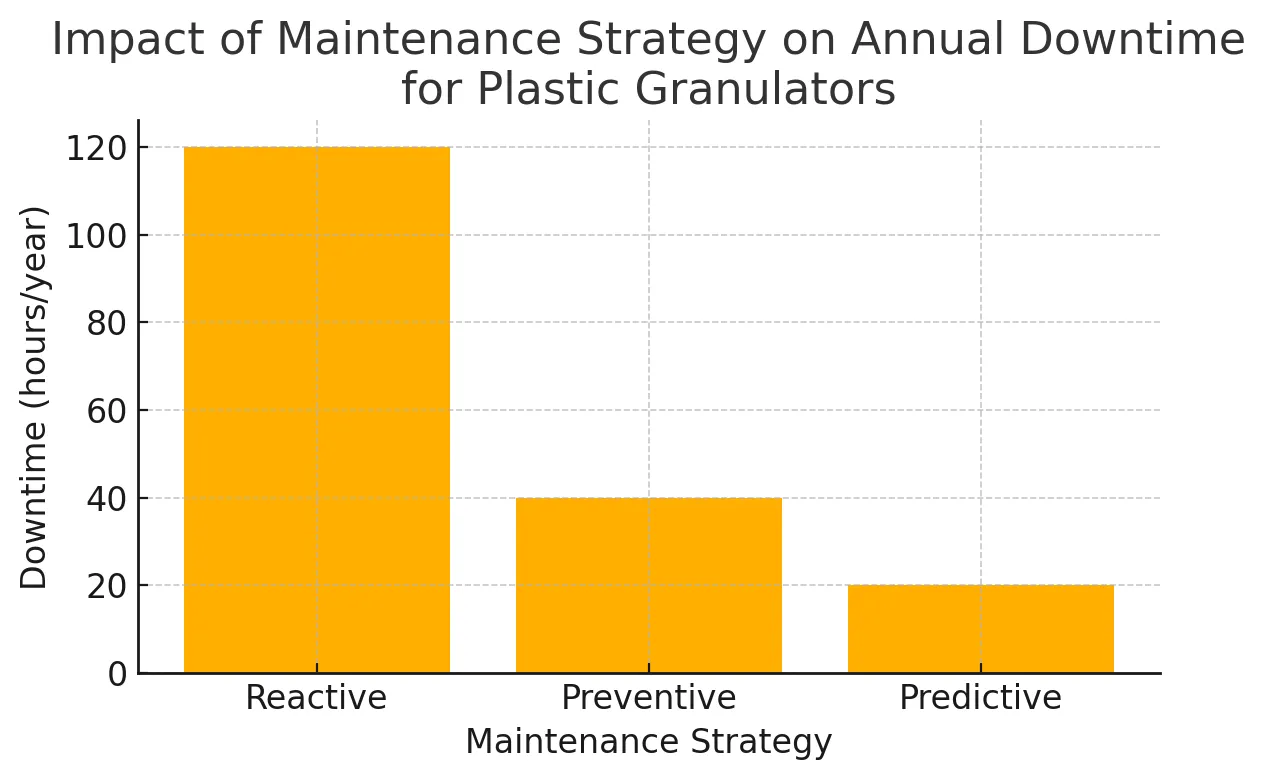
Principais benefícios comerciais
KPI | Manutenção Reativa | Manutenção preventiva | Preditivo (baseado em sensor) |
---|---|---|---|
Tempo de inatividade anual (horas)** | 120 | 40 | 20 |
Gasto com facas (US$ 1 TP 4 T/t) | $9.50 | $4.20 | $3.10 |
Consumo de energia (kWh/t) | 98 | 72 | 68 |
**Veja o gráfico de barras abaixo para uma comparação visual.
Verificações diárias – 5 minutos que economizam horas depois
- Limpeza visual – Remova as partículas finas ao redor do funil, da câmara de corte e da tela para evitar acúmulo de calor e flash.
- Ouça ruído e vibração – Um zumbido repentino geralmente indica desvio da folga da lâmina ou parafusos do rotor soltos.
- Condição da tela – Substitua imediatamente telas obstruídas ou deformadas; mesmo um bloqueio de 10 % pode aumentar a carga do motor em 15 %.
- Temperatura e amperes do motor – Registro e tendência; pontas sinalizam lâminas cegas ou deslizamento da correia.
- Intertravamentos de segurança – Teste os interruptores do portão e do funil no início do turno.
Tarefas preventivas semanais/mensais
Intervalo | Tarefa | Por que isso importa |
---|---|---|
Semanalmente | Verifique a tensão e o desgaste da correia de transmissão | Correias frouxas desperdiçam energia e aceleram o desgaste dos rolamentos. |
Verifique a folga entre a faca e a cama (0,10–0,25 mm típico) | A folga correta preserva a borda afiada e reduz a poeira. | |
Inspecionar os mancais do rotor para purga de graxa | Sinal precoce de lubrificação excessiva ou falha na vedação. | |
Mensal | Mancais de graxa (graxa especificada pelo OEM) | Evita superaquecimento e convulsão. |
Verifique o torque de todos os fixadores da câmara | Elimina o afrouxamento induzido pela vibração. | |
Inspecionar o gabinete elétrico: terminais, disjuntores | Descoloração causada pelo calor indica sobrecarga ou mau contato. |
Cuidados com lâminas e telas – O coração da retificação de alta qualidade
- Afie antes que o opacidade fique visível. Uma boa regra: afie a cada 40–60 h para lâminas finas e 80–100 h para lâminas grossas. As lâminas podem ser afiadas cerca de 10 vezes antes da troca.
- Utilize um gabarito de precisão. O passo pós-retificação deve corresponder às especificações do OEM para evitar danos irreversíveis ao rotor.
- Equilibre e combine conjuntos. Sempre instale facas como conjuntos correspondentes para manter o rotor equilibrado e limitar a carga do rolamento.
- Inventário de tela. Mantenha duas telas extras por máquina; aberturas danificadas distorcem o tamanho das partículas e geram partículas finas.
Controle de poeira e contaminação
O excesso de finos prejudica a extrusão e a injeção a jusante. Instale um desempoeirador ou ciclone em linha e esvazie os coletores diariamente. Verifique o fluxo de ar de extração; uma queda de 20 % dobra o arraste de finos.
Motor, caixa de engrenagens e sistema de transmissão
- Alinhamento de correias. Desalinhamento >2 mm reduz a vida útil da correia pela metade.
- Amostragem de óleo de engrenagem. A análise trimestral do óleo identifica a formação precoce de corrosão localizada.
- Partida suave ou VFD. Reduz a corrente de pico e o choque mecânico, prolongando a vida útil do motor.
Adotando a Manutenção Preditiva
Sensores de IoT acessíveis tornam o serviço baseado em condições realista até mesmo para pequenas plantas:
Sensor | Detecta | Alerta típico |
---|---|---|
Vibração (IMU) | Desgaste do rolamento, desequilíbrio do rotor | Velocidade RMS >6 mm/s |
Temperatura infravermelha | Superaquecimento do motor | Temperatura do estator >90 °C |
Transdutor de corrente | Picos de carga, facas cegas | +15 % acima da linha de base |
Alertas automatizados transferem equipes do combate a incêndios para trocas proativas de facas, eliminando paradas não planejadas.
Fluxo de trabalho do granulador de plástico – onde a manutenção se encaixa
O carrossel de imagens acima percorre uma linha de granulação típica, destacando os pontos de controle (tremonha, câmara de corte, plataforma de peneiramento, soprador de descarga). Use-o como um auxílio visual ao treinar operadores.
Impacto no desempenho da estratégia de manutenção
O gráfico abaixo ilustra como o tempo de inatividade diminui à medida que você passa da manutenção reativa para a preditiva.
(Gráfico exibido acima)
Use o delta do tempo de inatividade para construir seu caso de ROI: cada hora que um granulador de 75 kW fica ocioso custa ≈ US$ $180 em perda de produtividade e mão de obra.
Crie seu próprio cronograma de manutenção
- Comece com as recomendações do OEM e ajuste à sua mistura de materiais (PP abrasivo com fibra de vidro vs. LDPE macio).
- Registre tudo – horas de faca, trocas de tela, trocas de correias. Uma planilha simples ou um CMMS funcionam.
- Treine e capacite operadores. 80 % de falhas apresentam sintomas precoces que a equipe de linha consegue identificar.
- Guarde peças de reposição essenciais. Mínimo: conjunto completo de facas, duas telas, kit de correia de transmissão, graxa, mancais principais.
Segurança em primeiro lugar
Sempre siga as instruções de bloqueio/etiquetagem (LOTO) antes de entrar na câmara de corte. Verifique se há energia armazenada zero – correias, volantes e tampas hidráulicas conseguem reter força mesmo com a energia desligada.
Conclusão – Cinco Lições
- Um plano preventivo documentado reduz o tempo de inatividade em >60 %.
- Facas afiadas e com espaçamento adequado são o seu melhor aliado na produtividade.
- Inspeções de correias, rolamentos e telas levam minutos; negligência custa dias.
- O controle de poeira e a tendência da carga do motor melhoram a qualidade do produto e o uso de energia.
- As tecnologias de manutenção preditiva agora são acessíveis – comece aos poucos com sensores de vibração.
Ao integrar essas práticas, os compradores e as equipes técnicas garantem que seus investimentos em granuladores ofereçam qualidade de moagem consistente, custos operacionais mais baixos e tempo de atividade máximo.