Recycling News
In today's fast-paced world, where data security is a top priority, industrial shredders have become an essential tool for businesses across industries. Whether you're looking to dispose of sensitive documents, shred plastic waste, or destroy electronic media, choosing the right industrial shredder is crucial to ensure efficient and effective material processing. With a wide range of options available in the market, it can be overwhelming to navigate through the choices and determine the perfect shredder for your needs. This comprehensive guide aims to demystify the selection process, equipping you with the knowledge needed to make an informed decision.
Shredders play a pivotal role in the recycling industry, especially when it comes to processing film and fiber waste. These machines not only enhance the efficiency of recycling processes but also significantly contribute to sustainability efforts. Let's delve into the various applications of shredders in recycling film and fiber, and their impact on our environment.
Selecting the right shredder for film and fiber waste can be a daunting task given the variety of options available. This guide aims to provide you with practical tips on choosing the best shredding equipment tailored to your specific needs. We will cover factors such as material type, volume, and desired output, along with recommendations for top brands and models.
Most Durable, Versatile, and User-Friendly Plastic Shredder Available
Rumtoo plastic shredders are the top choice for both plastics recyclers and processors due to their unparalleled flexibility, versatility, ease of operation, durability, and low-maintenance design.
Plastic pelletizers are incredibly versatile machines used in the recycling and manufacturing industries to process various types of plastics. These machines convert plastic waste into small, uniform pellets that can be easily reused in new products. Below, we'll explore the most common types of plastics that can be effectively processed using a pelletizer.
In today's digital age, electronic devices are integral to our daily lives, but as they reach the end of their usefulness, they often become a security risk. E-scrap, or electronic waste, includes a variety of devices and media that can contain sensitive and confidential information. This is where the importance of an e-scrap shredder comes into play.
Unlocking the Full Potential of Aluminum Recycling with Rumtoo’s Specialized Shredding Systems
Recycling aluminum is essential not only for its environmental benefits but also for its economic value. However, aluminum often comes combined with other materials like plastics, complicating the recycling process. Rumtoo’s aluminum shredders are expertly designed to tackle these challenges, making them a leading choice for industries involved in aluminum recycling. These shredders don't just cut; they liberate aluminum from other materials, allowing for effective separation and maximizing the recycling value.
Our advanced single-screw plastic pelletizing machines with Heat Wave Stabilization™ produce premium plastic pellets by providing uniform heat distribution throughout the entire barrel length. This energy-saving pelletizer, available in both single or double stage arrangement, comes standard with hydraulic-powered screen change to ensure there is no downtime throughout each operating session.
Introduction
Recycling tires is a significant challenge that requires specialized equipment designed to handle the tough, durable nature of waste rubber. With millions of tires discarded annually, the importance of efficient tire recycling cannot be overstated. Rumroo, a global leader in tire shredding technology, offers innovative solutions that not only make tire recycling easier but also maximize the value of the end products. In this article, we'll delve into how Rumroo's tire shredders are specifically designed to recycle tires and the unique advantages they offer.
Our PP / PE plastic film water-ring pelletizing system integrates the functions of crushing, compacting, plasticization, and pelletizing all in a single step. At the heart of this system is our highly efficient single screw extruder with advanced heat stabilization technologies resulting in superior quality pellets that help to enhance your bottom line.
In addition to pelletizing plastic films, this system can also be utilized for raffias, filaments, bags, woven bags, and re-pelletizing of densified materials. The final products produced by this pelletizing system are in the form of pellets or granules that can be directly used in production lines for film blowing, pipe extrusion, and plastics injection, etc.
Working Principle
- Feeding: As a standard design, plastic scraps such as film and raffias are conveyed into the compacting room through a belt conveyor; to handle rolls’ scraps, a roll hauling-off device is an optional feeding method. The feeding speed of the conveyor belt or roll hauling-off is fully automatic based on how full the compactor’s room is. A metal detector can be integrated with the belt conveyor and can interlock with the control system to alert and halt the system in case metal is detected in the feeding section.
- Shredding and compacting: The rotary blades of the compactor will cut up incoming scraps. Frictional heating caused by high-speed rotary blades will heat and shrink the scraps just below their agglomerating point. Optimally designed guide structures compact the material and direct it into the extruder screw. It crushes, dries, and compacts the material, which enables a rapid and stable feeding from the compactor directly into the extruder.
- Plasticization and degassing: A specialized single screw extruder is applied to gently melt the pre-compacted material. The plastic scraps will be thoroughly melted and plasticized in the first stage extruder, and the plastic will be extruded by the second stage extruder. With a double-zone vacuum degassing system, volatiles such as low molecular compounds and moisture will be removed efficiently, making it especially suitable for heavily printed film and material with some water content.
- Melt filtration: Segmented filtering principle is used, with preliminary filtering in the first extruder and fine filtering in the second extruder, to reduce the frequency of changing filtering sieves. The requirements for the filter technology depend on the quality of the input material as well as the planned use of granules.
- Water-ring Pelletizing: Die-face water-ring pelletizing system is set as the standard granulating method. Advanced dewatering vibration sieve combined with horizontal-type centrifugal dewatering presents high-performance dried pellets.
Technical Specifications
Model Size | Efficiency Volume (Liter) | Motor Power (KW) | Diameter of screw (mm) | L/D | Motor Power (KW) | Throughput Rate (kg/h) |
---|---|---|---|---|---|---|
SJ80 | 300 | 37 | 80 | 36 | 45/55 | 160-220 |
SJ100 | 500 | 55 | 100 | 36 | 90/110 | 300-380 |
SJ120 | 800 | 90 | 120 | 36 | 132 | 450-480 |
SJ140 | 1000 | 110 | 140 | 36 | 160/185 | 500-650 |
SJ160 | 1200 | 132 | 160 | 34 | 220/250 | 800-1000 |
SJ180 | 1400 | 315 | 180 | 34 | 315 | 1000-1200 |
Additional Images
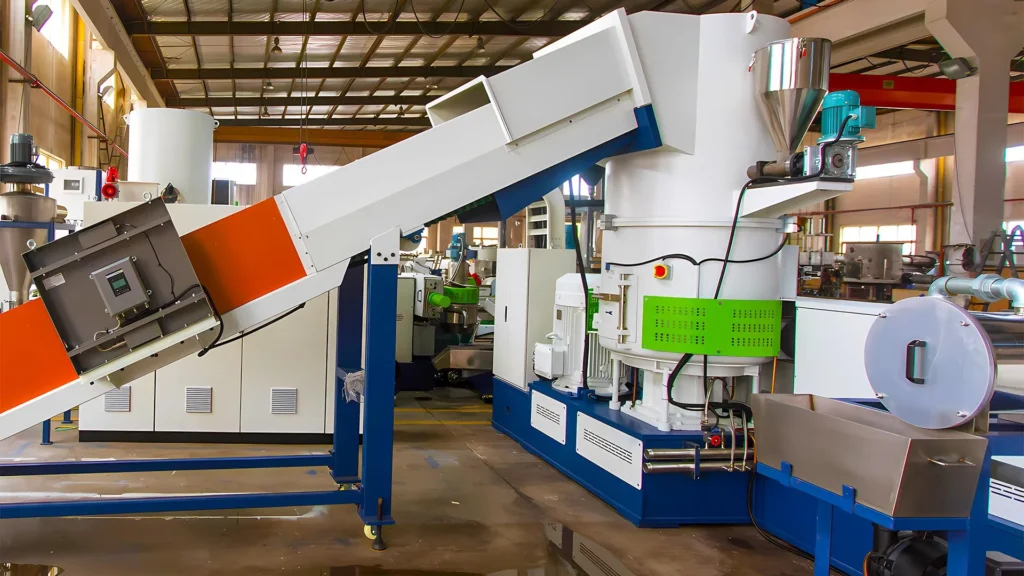
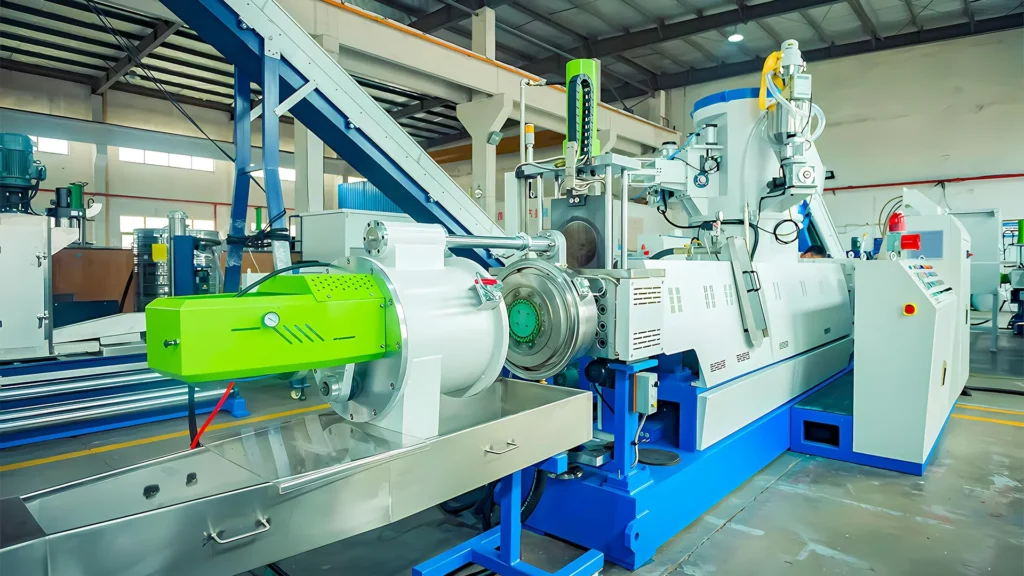
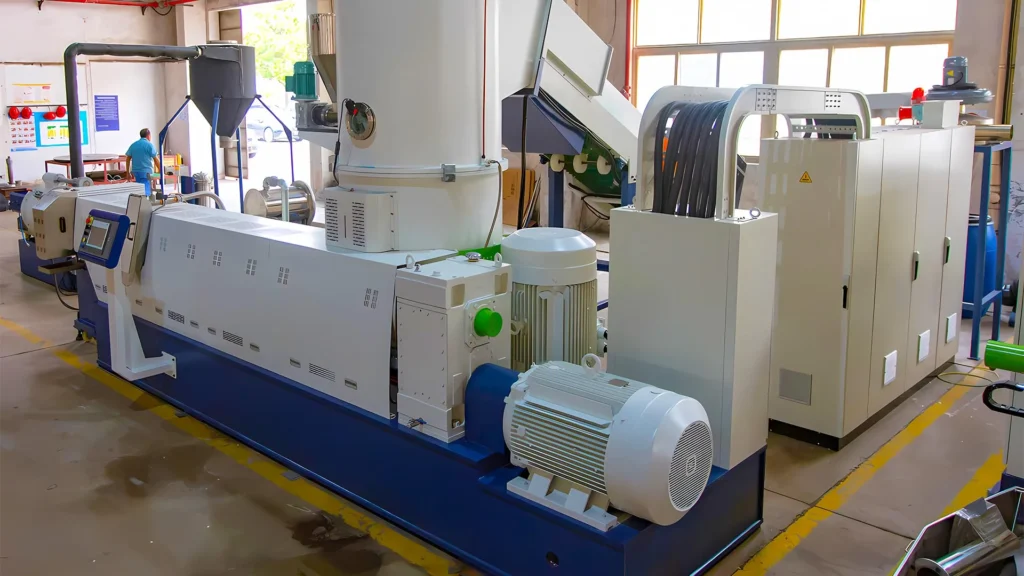
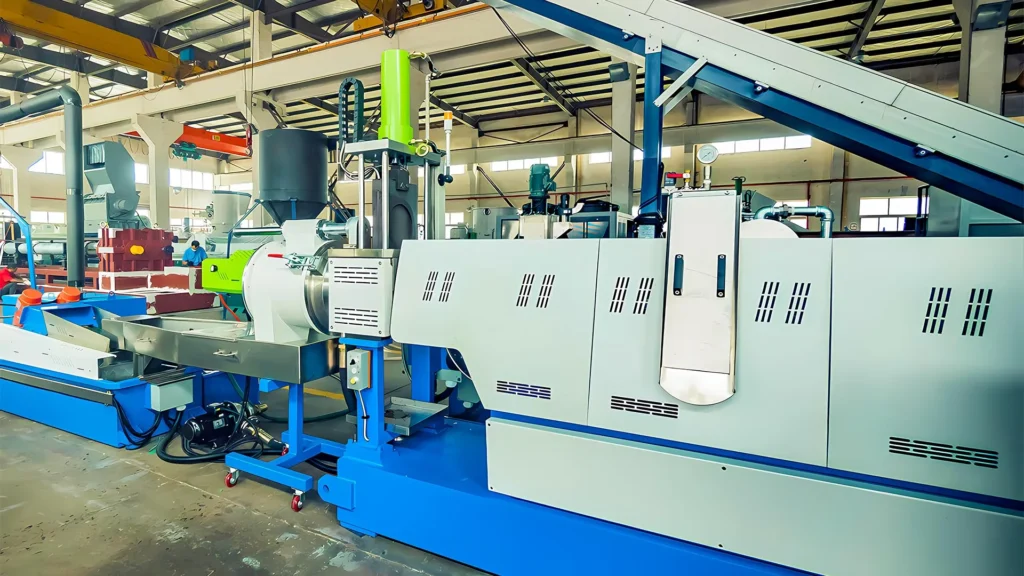
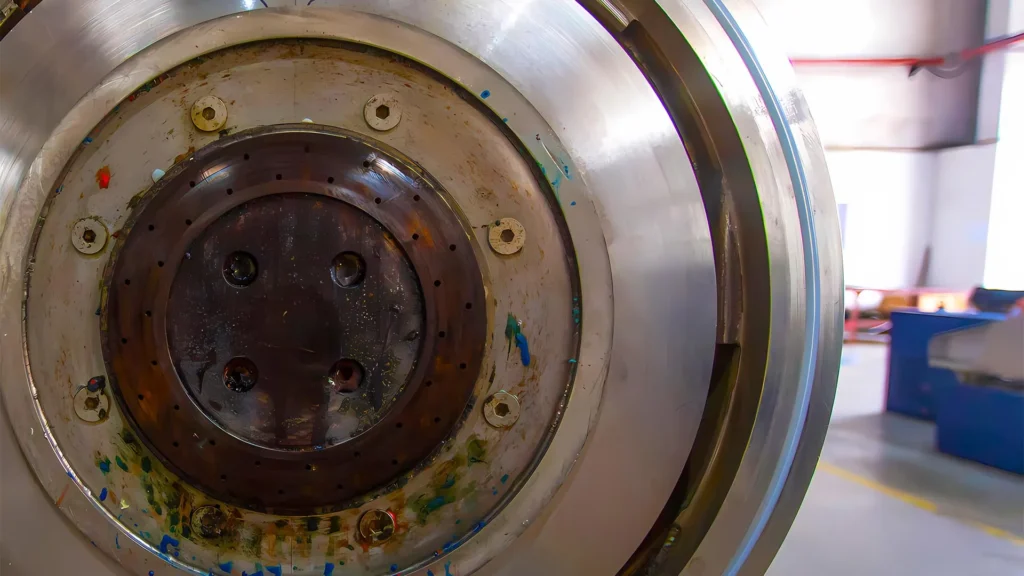
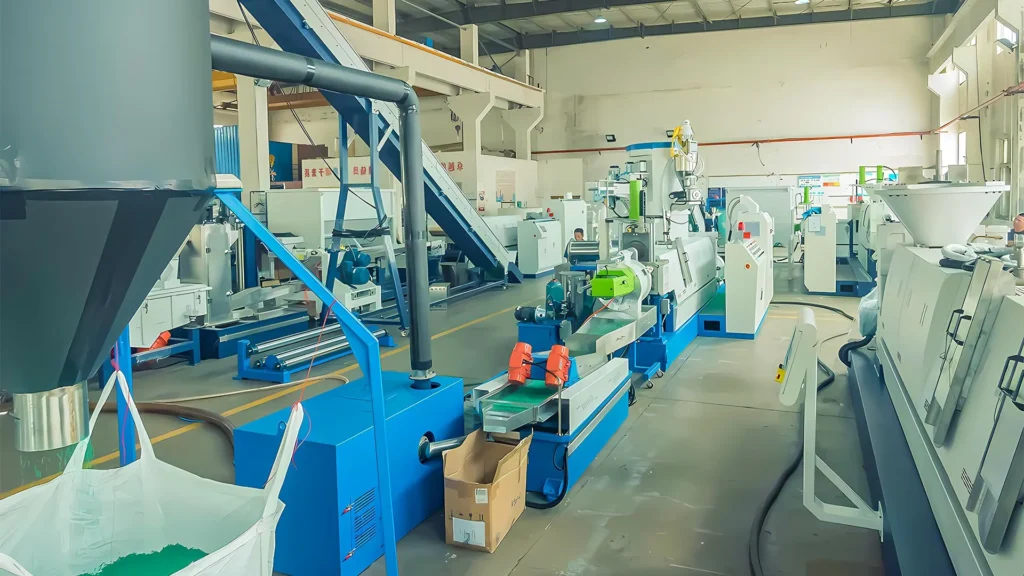
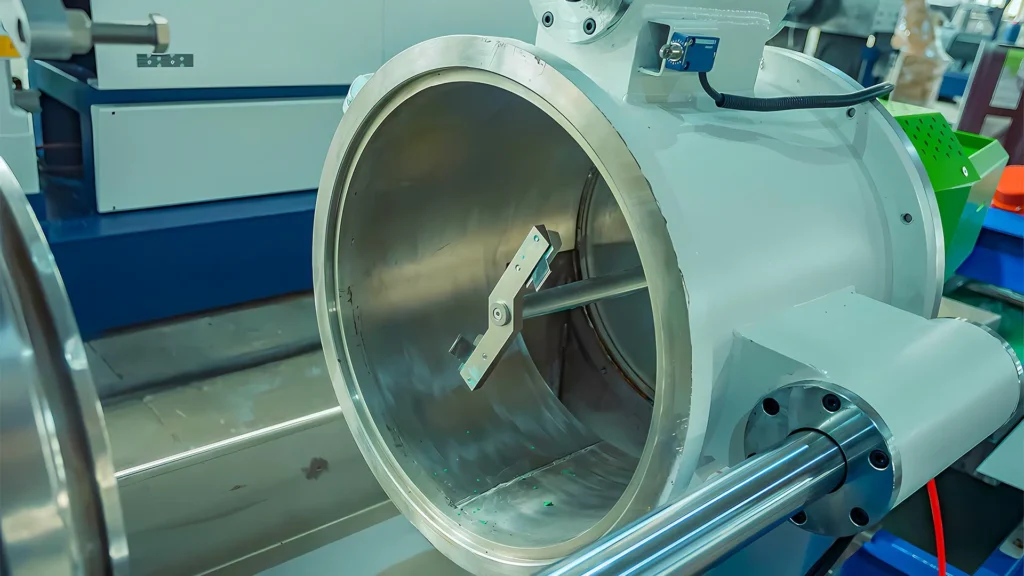
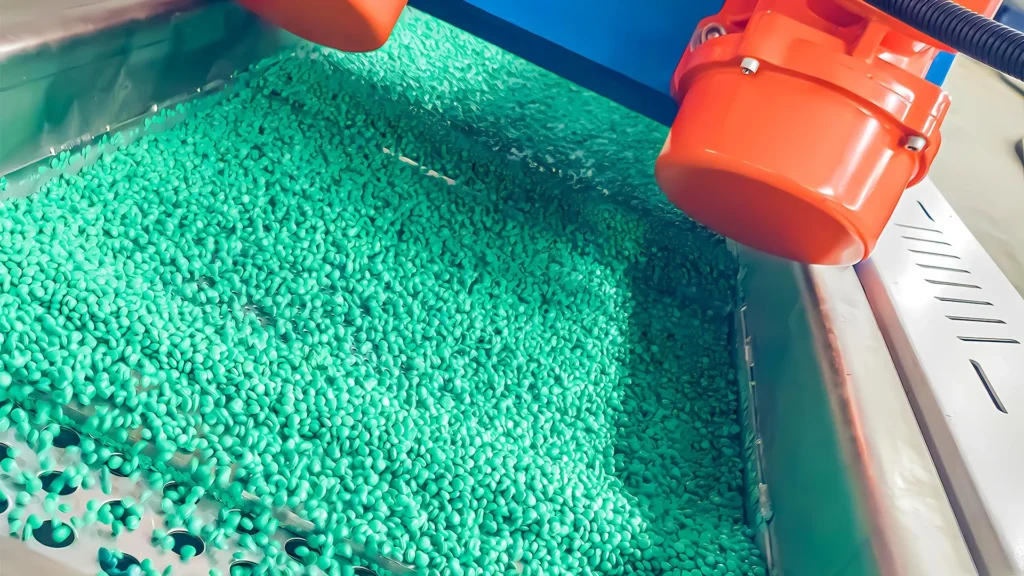