Sustainable Cleanliness: Eco-Friendly Recycling Washing Solutions
Recycling Washing Systems
Clean Cycle: Advanced Recycling Washing Systems
Wash & Reuse: Maximize Recycling with Our Systems
Pollution Fighters: Washing for a Cleaner Future
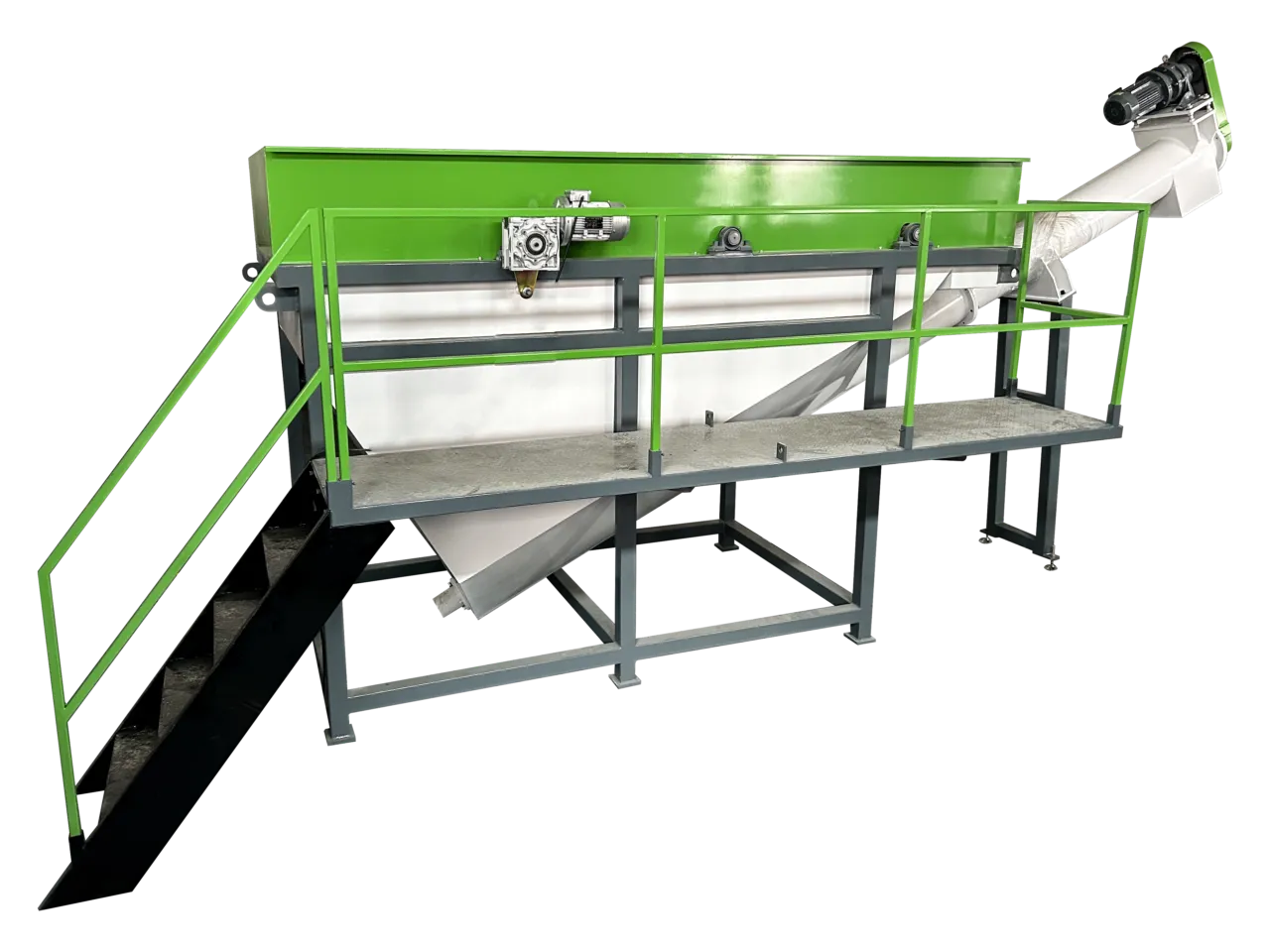
Sink-float separation tanks are essential components in plastic recycling. They play a key role in cleaning and sorting plastic materials that are denser than water, such as PET, PVC, and PS. These tanks combine washing, separation, and sediment removal in a single system, streamlining the recycling process and improving material purity. Here’s a detailed look at their functions, features, operation, and benefits.
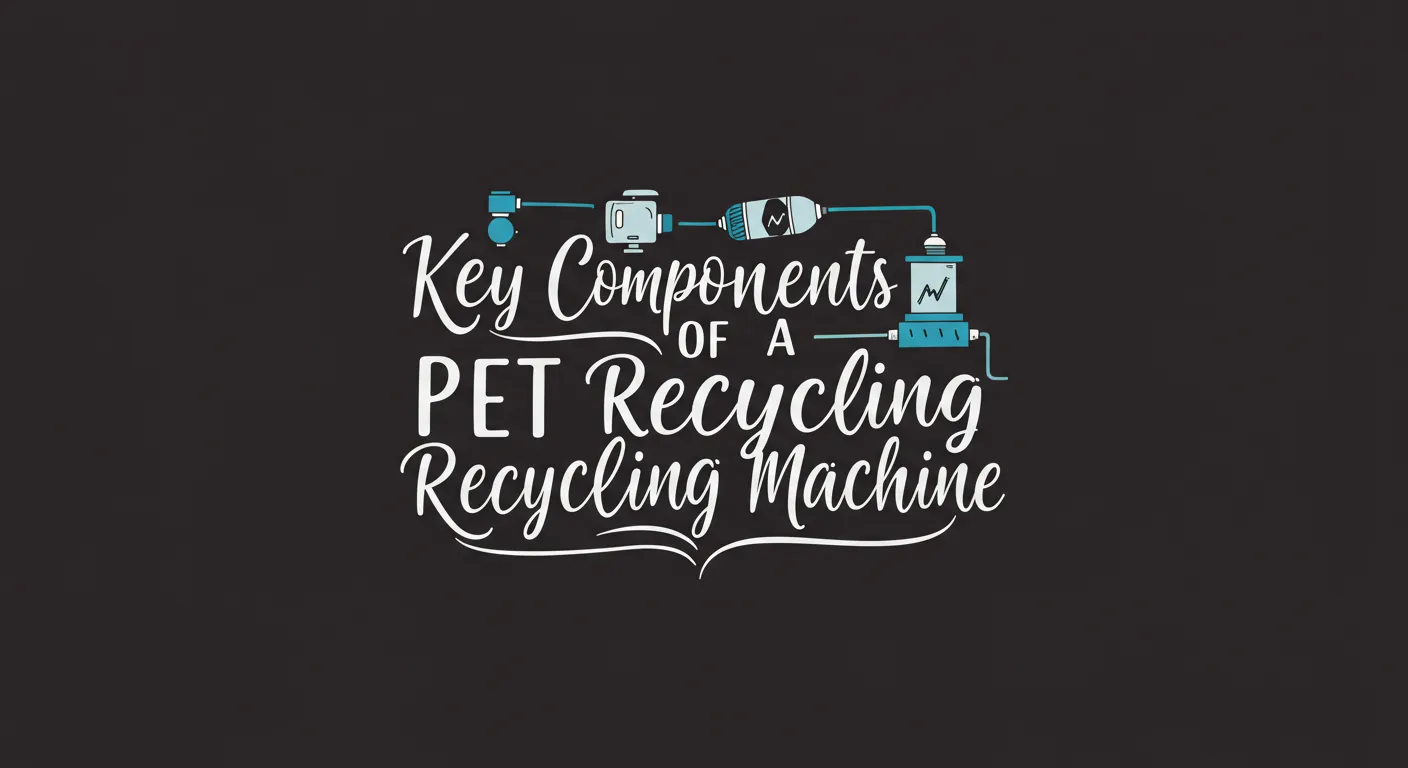
Addressing the global challenge of plastic waste, polyethylene terephthalate (PET) stands out due to its widespread applications and recyclability. Efficient PET recycling systems are crucial for realizing a circular economy and reducing reliance on virgin resources. This article provides a professional overview of the core components of a PET recycling machine, elucidating how these essential modules work in concert to transform post-consumer PET materials into high-quality recycled feedstocks. We will delve into the equipment configurations of critical stages including pre-processing, washing, sorting, and extrusion pelletizing, briefly analyzing the technical specifications and performance metrics of each section. This aims to offer industry professionals a deeper understanding of the PET recycling process flow and equipment composition.

In the realm of environmental preservation, plastic recycling plays a pivotal role. Among various recycling methods, the PP PE film shredding and densifying line has emerged as a game-changing technology. This innovative process transforms dirty bales of PP/PE films into densified products, ready for chemical application or conversion into plastic granules through pelletizing.
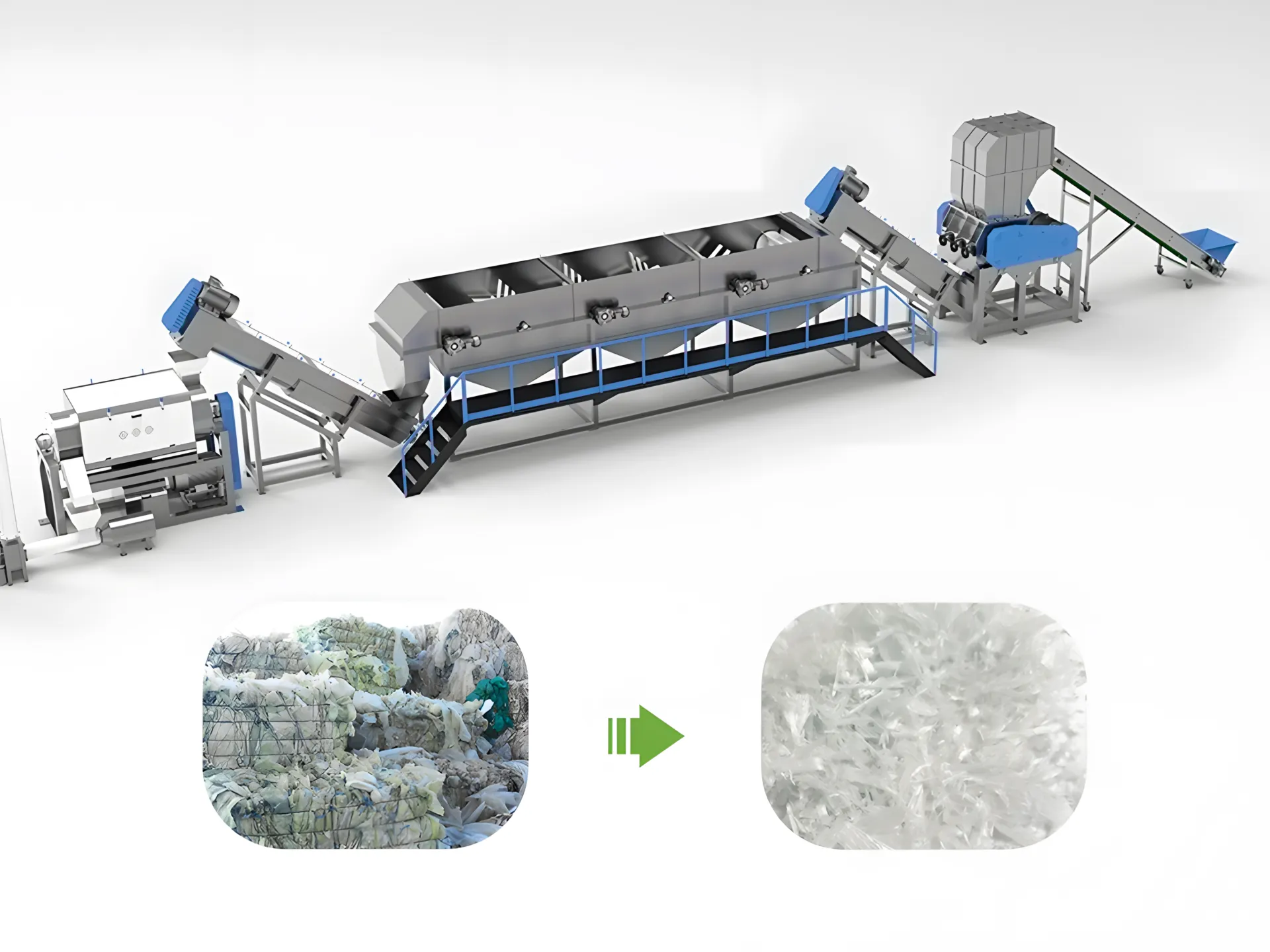
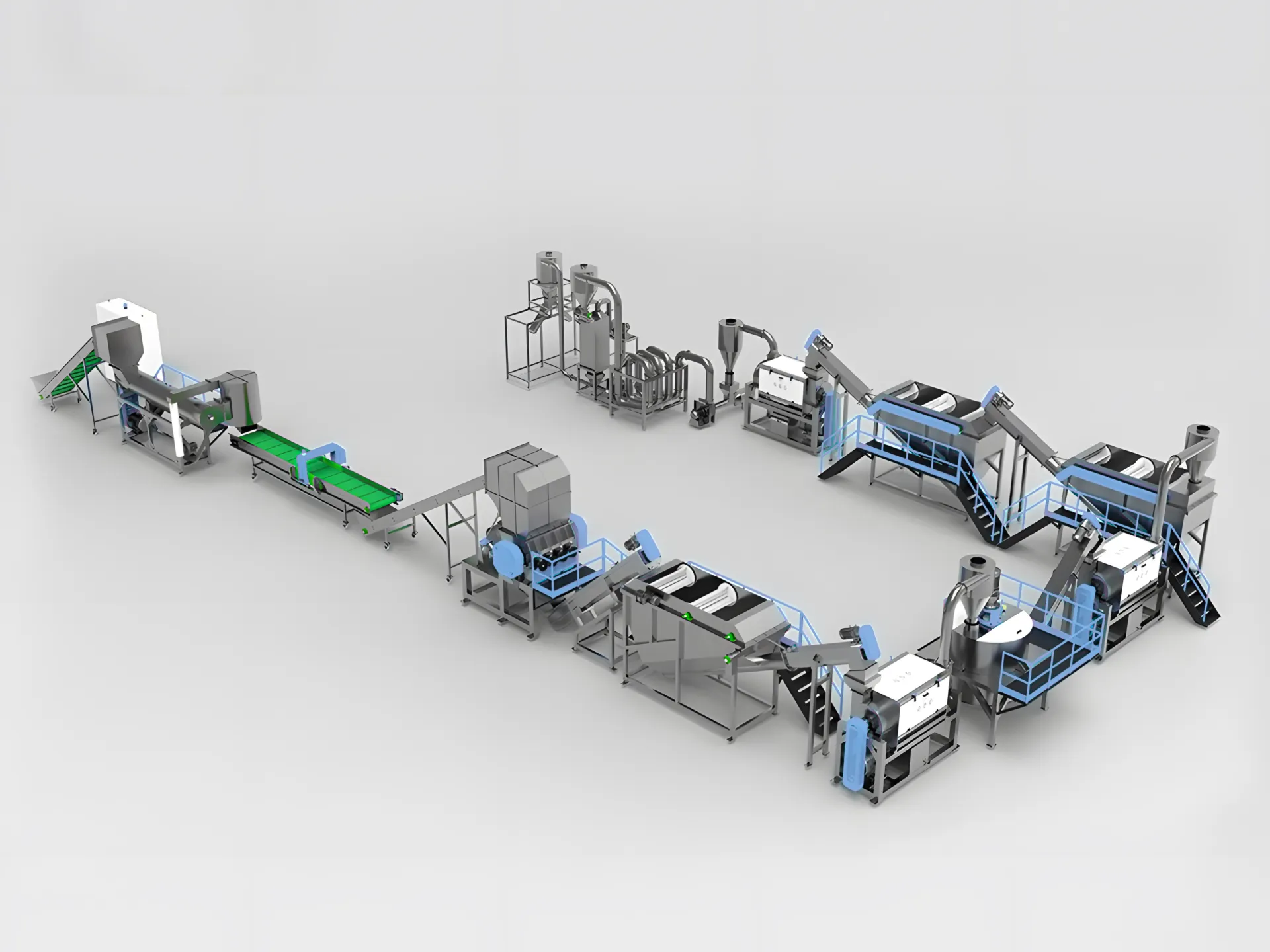
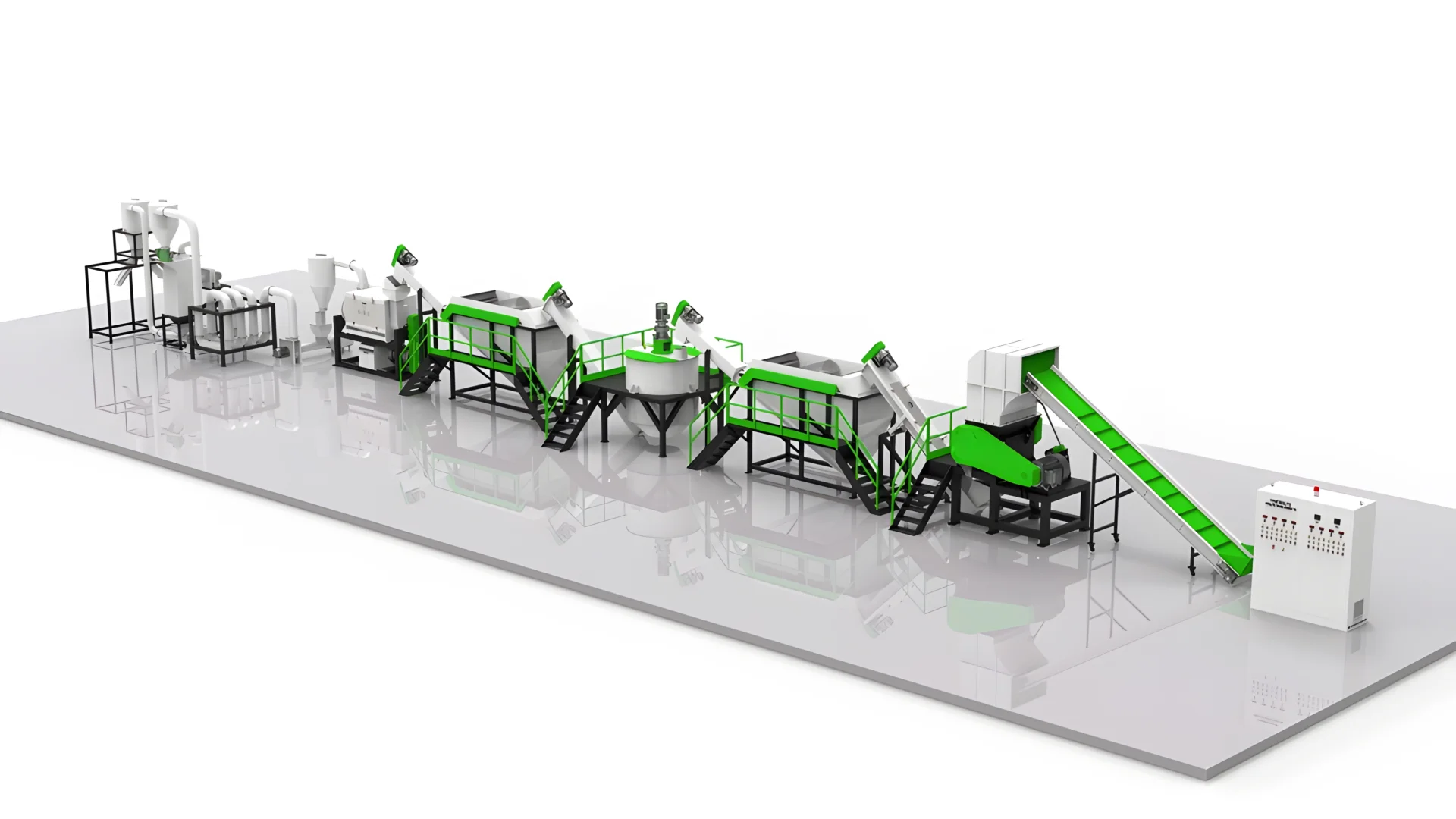
High-density polyethylene (HDPE) and polypropylene (PP) are widely utilized across various sectors, presenting challenges in disposal due to their bulky and complex nature. To tackle this, we proudly introduce our HDPE and PP Rigid Plastic Shredding Recycling Line.
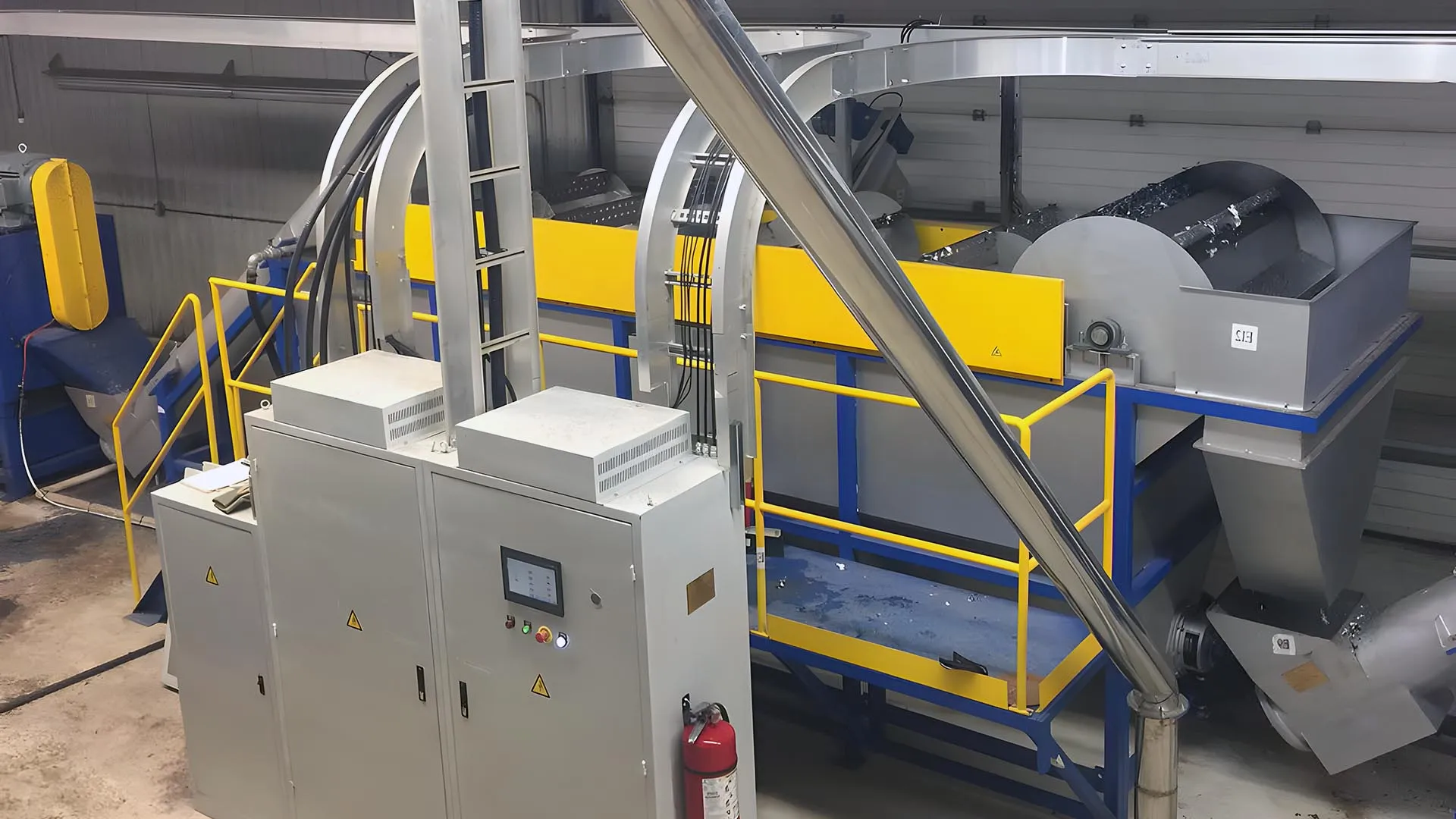
The entire line is designed to clean shredded PP/PE regrind, featuring a friction washer, floatation tank, centrifugal dryer, squeezer, extruders, and pellet cutting system. Below are explanations for some of the key machines:
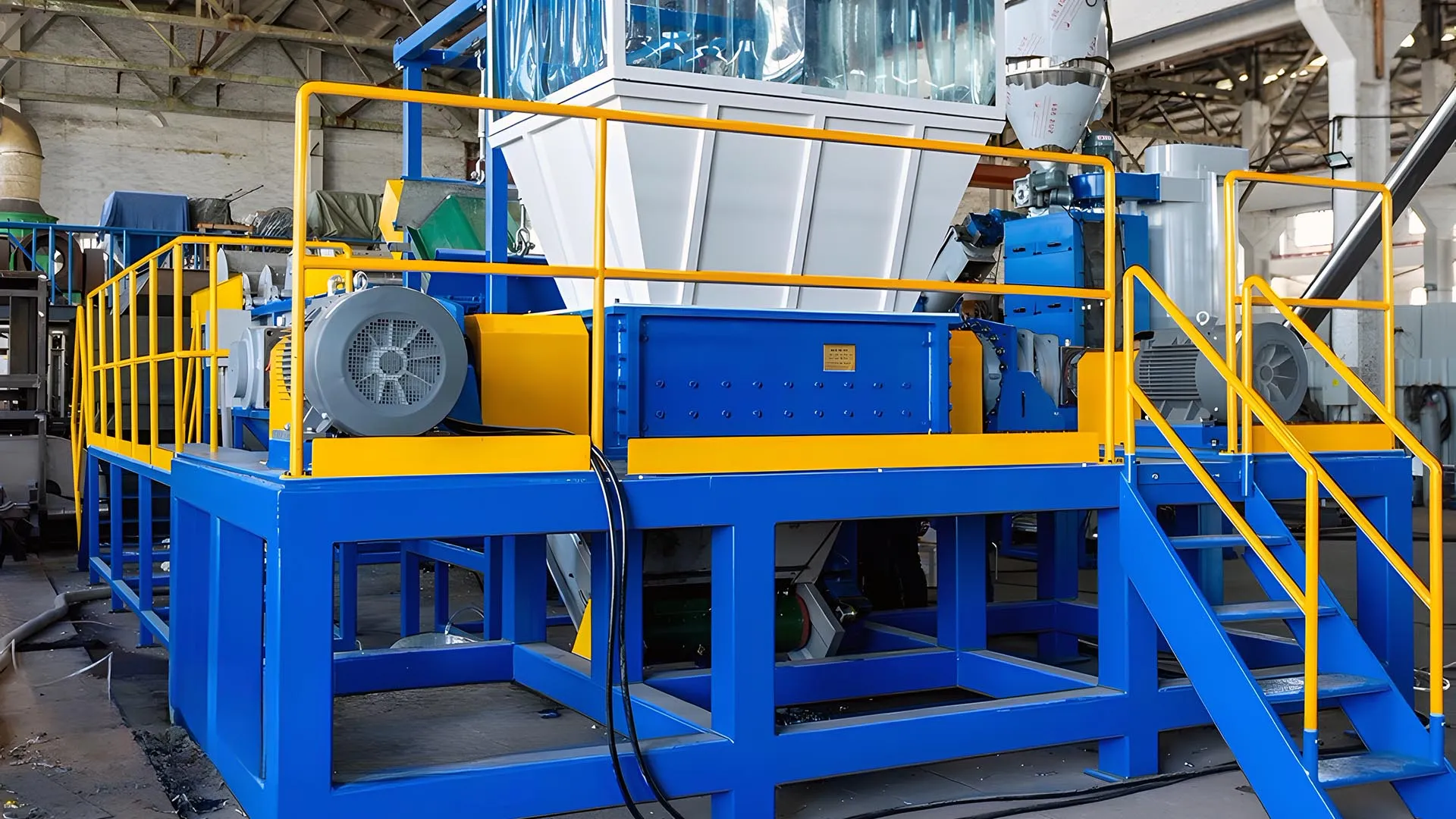
This HDPE, PP, and PS rigid plastic washing plant is designed to thoroughly clean contaminated rigid plastics, including HDPE/PP bottles, lumps, and other rigid materials. This comprehensive recycling solution includes a robust shredder with an overhead magnet, granulator, sink-float separation tank, centrifugal dryer, thermal dryer, zig-zag separator, and a dual-bag filling station. The resulting premium-quality plastic flakes can be reused in manufacturing plastic products.
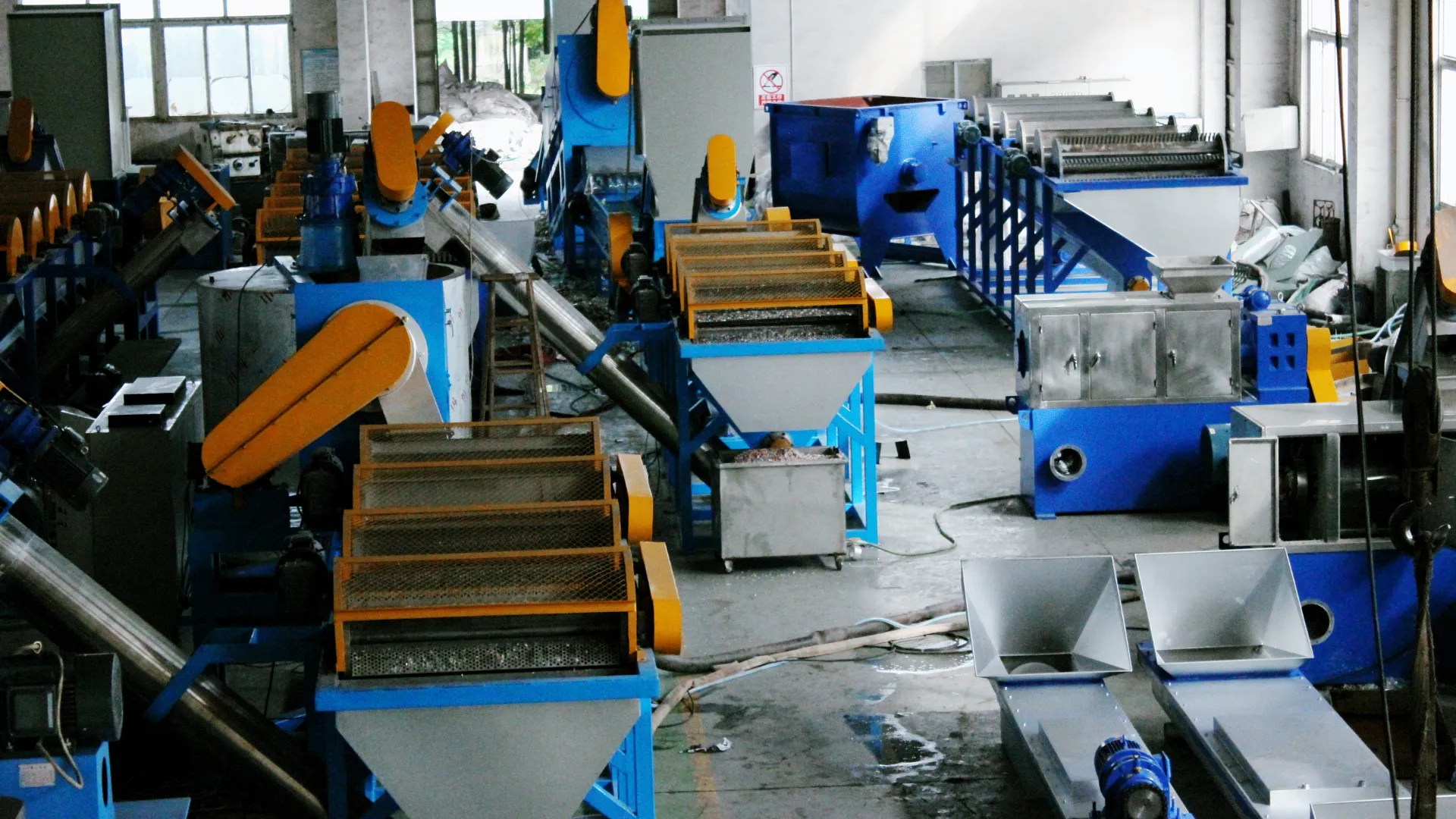
This is our standard 500 KG/H PET bottle washing line, specifically designed for our clients in the United States. Employing the most advanced technology and equipment, this line ensures efficient and high-quality PET bottle recycling processes. Our washing line features comprehensive capabilities that meet stringent environmental and production standards, aimed at providing our clients with the best recycling solutions and maximum economic benefits. Additionally, we offer customization services to accommodate diverse operational needs and site conditions for each client.