A wet crusher & granulator is an essential piece of equipment designed specifically for plastic recycling operations. By simultaneously crushing plastic waste into smaller particles and cleaning it with water, it significantly enhances recycling efficiency and produces higher-quality granules suitable for reuse.
In this article, we delve deeply into what a wet crusher & granulator is, how it operates, its notable advantages, and why it is increasingly indispensable in the plastic recycling industry.
What is a Wet Crusher & Granulator?
A wet crusher & granulator combines the processes of crushing, granulating, and washing plastic waste into a single operation. Unlike conventional dry granulators, which only reduce the size of plastics, this machine integrates water directly into the cutting chamber. This approach removes contaminants such as dirt, labels, adhesives, and residual chemicals while crushing the plastic into uniform granules.
Commonly processed materials include:
- PET bottles
- Plastic films and bags
- Rigid plastics (e.g., crates, buckets)
How Does a Wet Crusher & Granulator Work?
The machine operates at high rotational speeds (typically between 400-600 RPM) using heavy-duty cutting knives crafted from durable materials like D2 steel. During operation, water sprays continuously into the cutting chamber, offering the following benefits:
- Cooling the cutting chamber, preventing overheating.
- Cleaning the plastic waste, removing contaminants efficiently.
- Lubricating the blades, reducing friction, and prolonging component life.
Crushed materials pass through a screen filter, producing granules ranging from approximately 10mm to 100mm, customizable according to recycling requirements.
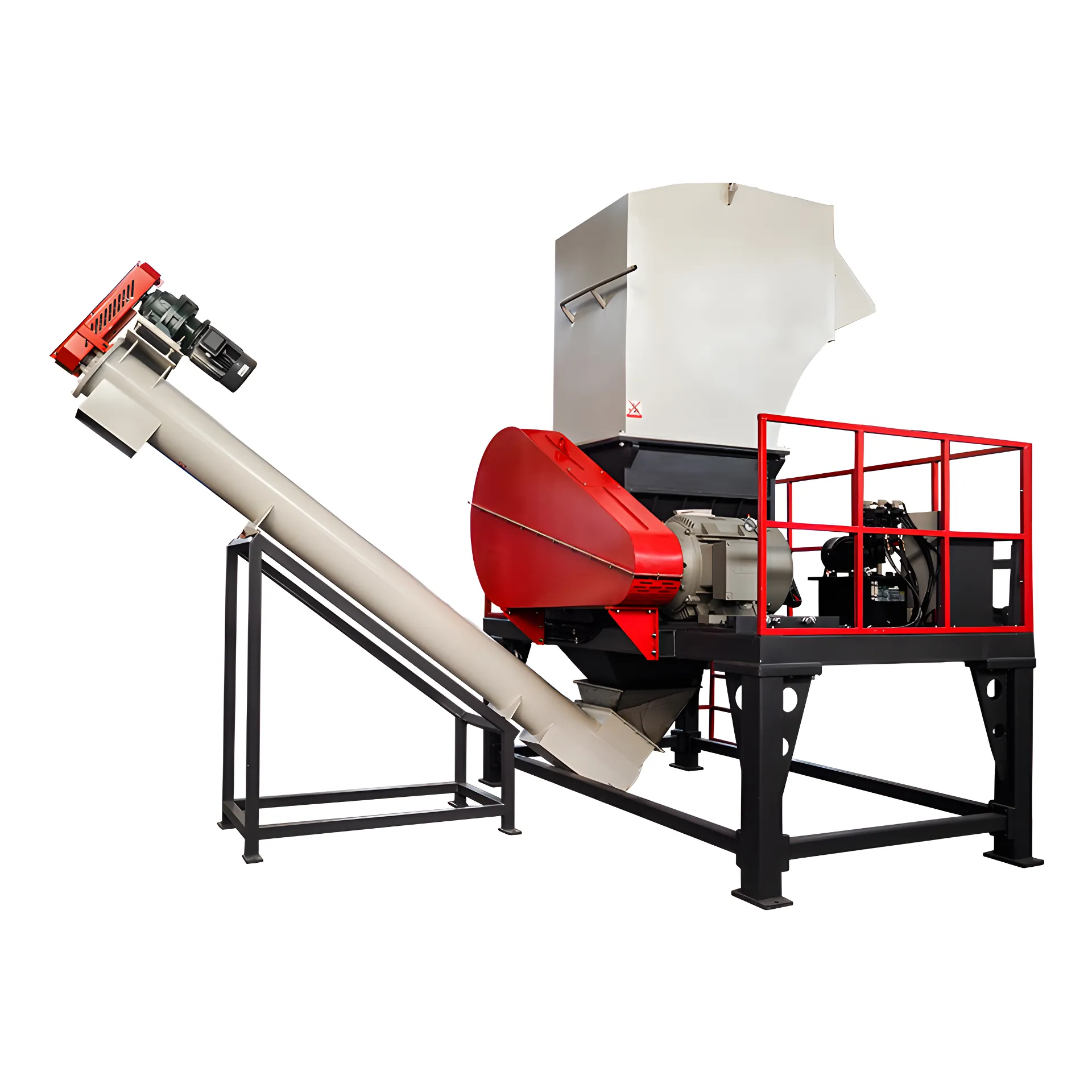
Key Advantages of Using a Wet Crusher & Granulator
Implementing a wet granulation process offers substantial benefits compared to dry methods, including:
Improved Quality of Granules
- The simultaneous washing and crushing process results in cleaner and more uniform granules, enhancing their value for reuse and recycling.
Reduced Dust and Pollution
- Water significantly reduces airborne dust and fines generated during crushing, leading to cleaner operational conditions and improved workplace safety.
Extended Equipment Life
- The continuous cooling and lubrication provided by water reduce frictional heat, protecting components such as bearings, knives, and internal chamber surfaces, thus minimizing maintenance requirements.
Efficiency and Cost Savings
- Combining washing and granulation into one step reduces processing time, labor, and energy costs, streamlining the recycling workflow and improving overall productivity.
Applications in Plastic Recycling
The wet crusher & granulator is particularly effective in recycling scenarios that require thorough cleaning alongside size reduction, including:
- PET Bottle Recycling: Transforming post-consumer PET bottles into high-quality flakes suitable for manufacturing new bottles or fiber products.
- Plastic Film Recycling: Processing plastic films, wraps, and bags, often heavily contaminated, to produce clean and reusable material.
- Rigid Plastic Recycling: Granulating rigid plastics such as crates, buckets, and pallets, achieving consistency for downstream applications.
Its versatility ensures it meets diverse recycling needs across various plastic materials, contributing significantly to sustainable recycling practices.
Broader Context and Industry Differences
While predominantly utilized in plastics recycling, “wet granulation” also appears in other industries, including pharmaceuticals and chemical processing. However, the combination of crushing and water-assisted granulation as detailed here is unique to the plastic recycling sector. In pharmaceutical contexts, wet granulation typically refers to agglomeration techniques rather than mechanical crushing.
Conclusion: The Impact of Wet Crusher & Granulator on Sustainable Recycling
The wet crusher & granulator significantly improves the efficiency and effectiveness of recycling plastics by merging size reduction with washing, enhancing operational sustainability. Facilities adopting this advanced granulation technology can reduce operational costs, enhance product quality, and significantly contribute to a circular economy by facilitating higher-value recycled materials.
Understanding and leveraging this technology enables informed decisions, fostering more sustainable practices across the recycling industry as we move forward.